L’intégration du perçage profond dans les centres WFL
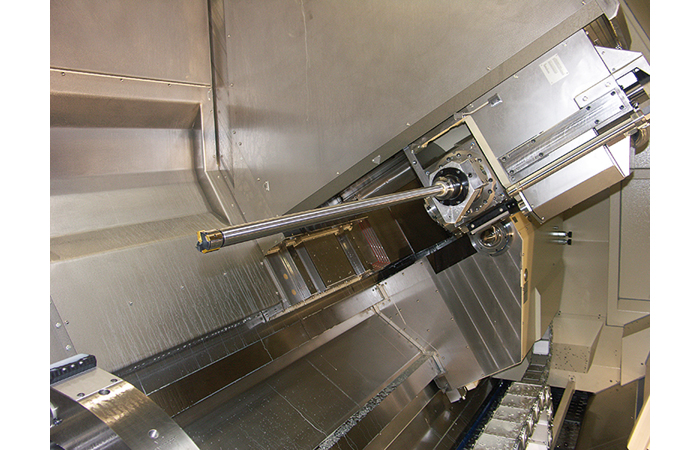
Le perçage profond est un cas particulier parmi les opérations d’usinage intérieur, posant des problèmes spécifiques. Des solutions encore plus pointues sont exigées dans des branches comme, par exemple, l’aéronautique, utilisant des matériaux et alliages spéciaux difficilement usinables.
On parle généralement de perçages profonds pour des perçages de 0,2 à 500 mm de diamètre, dont la profondeur compte au minimum trois fois la mesure du diamètre, ou pour les perçages plus petits à un rapport L/D ≤ 100. Dans des cas particuliers, il peut atteindre jusqu’à 400, selon le procédé utilisé et le matériau de la pièce. Un équipement spécifique en machines et en outils s’avère alors nécessaire à cette étape d’usinage, principalement en raison de d’enlèvement de copeaux.
Outils spéciaux
Les défis principaux pour réaliser des perçages profonds sont l’amenée de réfrigérant lubrifiant sur le tranchant, l’évacuation simultanée des copeaux et la création d’un trou aussi droit que possible. La tête de perçage est généralement composée d’un seul tranchant de coupe ou formée de plaques de coupe amovibles, d’un tranchant secondaire et de rails de guidage complémentaires. Cette structure assure l’appui du foret contre la paroi de perçage, permettant une précision supérieure et un meilleur centrage du foret pendant le processus, ainsi qu’une meilleure qualité de la surface du perçage.
En cas d’évacuation extérieure, on utilise le plus souvent des forets à une lèvre. Le réfrigérant lubrifiant est alors amené par des alésages d’alimentation dans le foret jusqu’au tranchant, et le mélange copeaux-réfrigérant-lubrifiant est évacué par une rainure longitudinale en V au niveau de l’outil. Ce procédé est généralement utilisé pour les perçages de 0,5 à 40 mm de diamètre. Pour des diamètres de perçage de 16 mm ou plus, il est possible d’employer le procédé BTA (Boring and trepanning association). Au cours de ce procédé, le mélange de copeaux-réfrigérant est évacué par l’intérieur, qui offre l’avantage que les copeaux n’entrent plus en contact avec la surface de perçage. Pour des diamètres à partir de 25 mm environ, il est possible d’employer des forets Ejector, une forme spéciale du foret BTA, conçue sur la base d’un système double tube et équipés d’orifices de sortie de réfrigérant lubrifiant sur la périphérie de la tête de perçage.
Usinage intégré
Le perçage profond est souvent un obstacle à l’usinage complet de pièces. Pourtant, cette opération forme une part essentielle de l’usinage de la majeure partie des pièces fabriquées sur les centres d’usinage du constructeur autrichien WFL Millturn de Linz, distribué en France par la société Mehrtech, qui porte de ce fait une attention toute particulière à ce sujet. « De nombreuses entreprises ne possèdent pas les machines adaptées et doivent sous-traiter cette étape d’usinage, ce qui allonge les temps d’usinage et augmente le risque d’imprécisions lié à la multiplication des serrages », observe Reinhard Koll, responsable des techniques d’applications chez WFL. Et Dieter Schatzl, directeur marketing d’ajouter : « Comme cela affecte bien évidemment le facteur économique. C’est précisément à ce point que nous répondons par l’intégration d’une fonction de perçage profond au cœur même de nos centres d’usinage. »
Dans le cas de perçages extrêmement profonds ou de matériaux difficilement usinables, on emploie souvent un procédé de perçage progressif, avec des outils de différentes longueurs mais de diamètre identique, afin de limiter l’usure des outils. Dans les machines Millturn WFL, tous les outils de perçage utilisés sont contenus dans le magasin d’outils, rendant possible un usinage profond complet sur six faces en un seul ou deux serrages.
De plus, WFL a intégré une surveillance du processus du perçage profond à la commande de la machine, assurant un résultat optimal, même pour des perçages individuels. « Le choix du lubrifiant jouant un rôle essentiel dans la sécurité du processus d’usinage et la qualité de surface des perçages, nos machines sont conçues pour répondre aux plus hautes exigences, que l’usinage se réalise avec des émulsions, de l’huile ou les deux réfrigérants lubrifiants. Nous pouvons couvrir tous les cas d’applications sur une plage de pressions de travail comprise entre 10 et 350 bar et un débit de refoulement de 10 à 800 litres », précise Reinhard Koll, en terminant.
à propos de WFL Millturn Technologies
les plus lus
à lire aussi
Les nouveaux produits
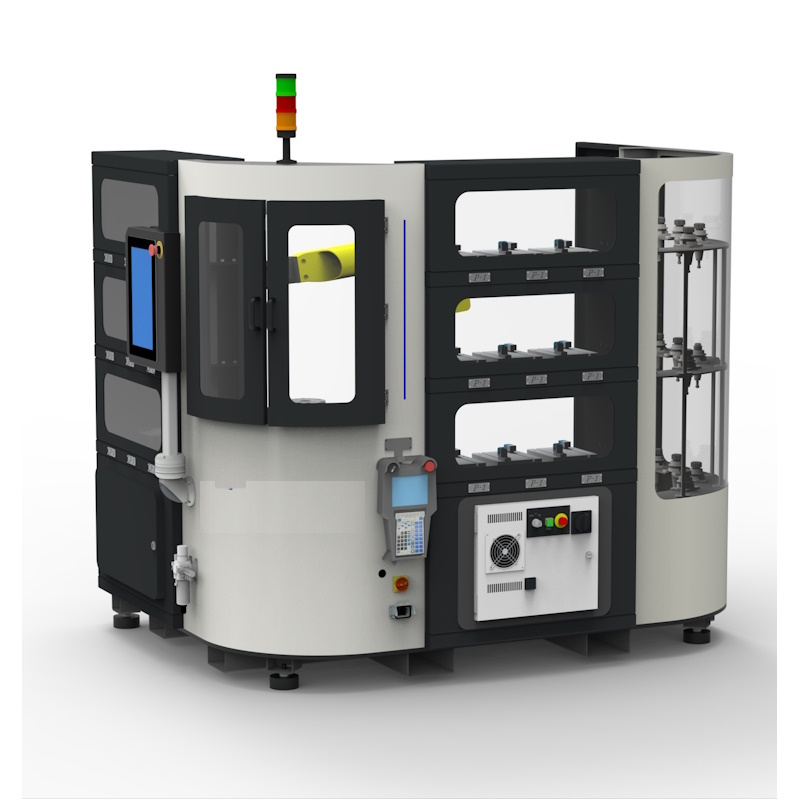
Robotique FANUC pour l'usinage pièces unitaires sur plateforme CUBEBOX
PALETTE, la station robotisée pour les palettes et les systèmes de serrage sur centres d'usinage