Du XXL pour l’usinage intégral
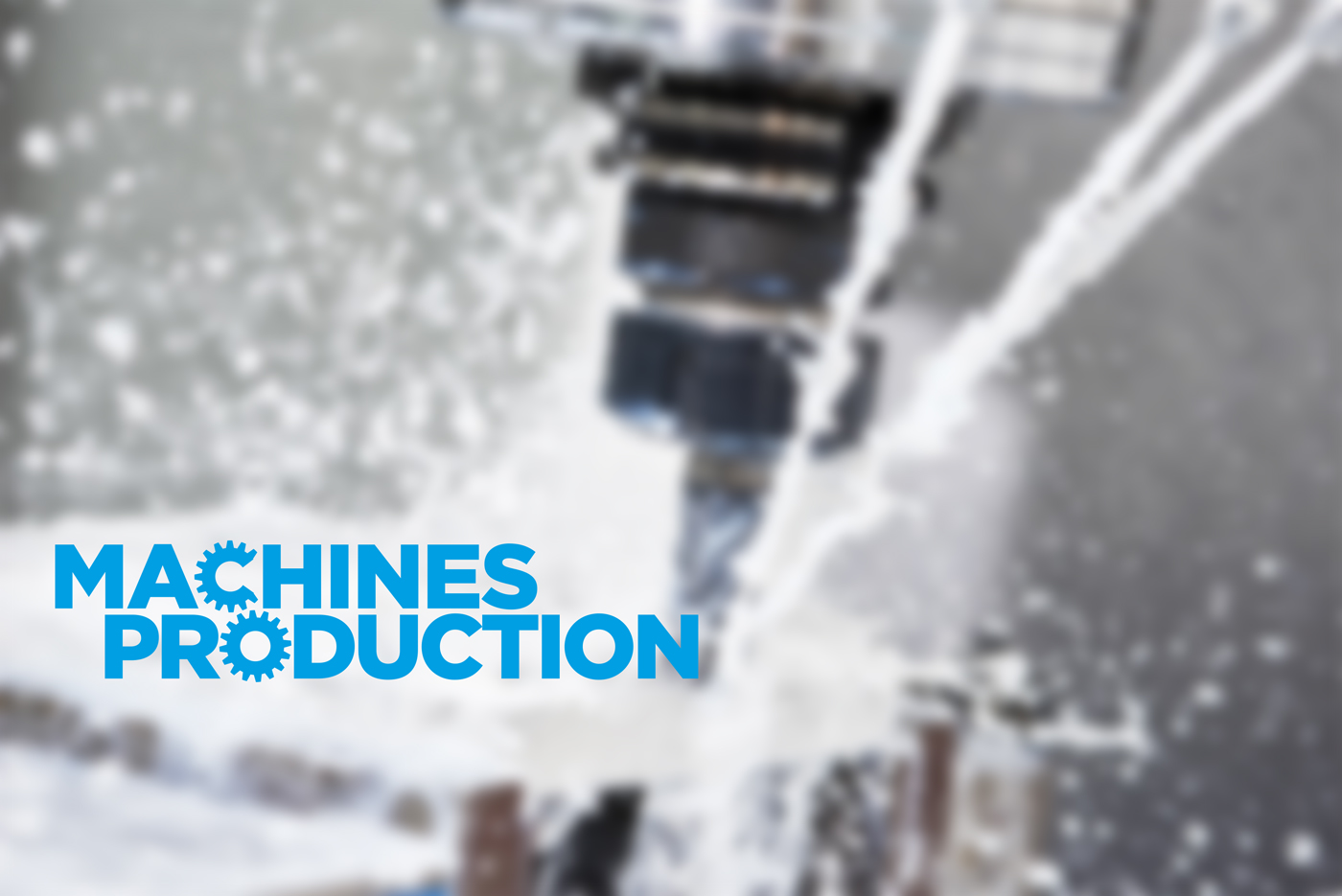
WFL Millturn Technologies GmbH & Co. KG se présente comme le seul constructeur spécialisé exclusivement dans la fabrication de tours-fraiseurs multifonctionnels. Depuis près de trois décennies, ses machines sont devenues dans nombre d'entreprises high-tech un outil indispensable pour la fabrication de composants complexes et ultra-précis.
Le constructeur a profité de ses récentes Portes Ouvertes sur son site de Linz en Autriche, pour présenter sa nouveauté mondiale, la machine M200, complétant la gamme Millturn vers le haut. Actuellement, la gamme de produits WFL compte 14 modèles différents proposant des longueurs de tournage de 1 000 à 8 000 mm et des diamètres de tournage de 520 à 1 500 mm permettent l’usinage intégral d’une large gamme de pièces. Le nouveau centre d’usinage élargit les capacités jusqu’à un diamètre de 2 000 mm et une longueur de 14 000 mm. Martin Kaukal, Directeur Commercial de WFL Millturn Technologies précise : » A partir d’aujourd’hui, les solutions d’usinage complet de notre gamme Millturn existante sont également disponibles pour les très grandes applications. C’est essentiellement pour des pièces grandes et chères que les avantages de l’usinage complet prennent de l’importance et offrent une meilleure productivité, une flexibilité insoupçonnée, ainsi qu’une plus grande précision tout en réduisant les coûts « .
Usinage en un serrage de très grandes pièces
La machine étant construite pour différentes longueurs de tournage et entre-pointes, elle peut notamment usiner des pièces jusqu’à 60 tonnes. Elle est adaptée aussi bien à l’usinage lourd qu’à l’usinage de finition de grande précision. Le spectre d’applications visées va des grands trains d’atterrissage, d’immenses vilebrequins, des arbres de turbines et de générateurs, des corps de vannes jusqu’aux arbres et cylindres de l’industrie lourde. La tête de tournage-perçage-fraisage peut traiter de façon productive des matériaux difficiles à usiner avec des valeurs de pointe de 80 kW et 1 800 Nm (100% ED). Grâce à la structure de la machine avec des composants en fonte absorbant les vibrations et dont la rigidité est optimisée, l’usinage s’effectue pratiquement sans aucune vibration. L’interface HSK-A125 standard fournie avec l’outil ainsi que le Capto C10 en option garantissent d’exploiter pleinement le potentiel de l’outil et la puissance de la broche. Des entraînements puissants assurent les forces d’avance les plus élevées et une dynamique unique pour une machine de cette dimension. L’axe B permet d’effectuer toutes sortes d’usinages inclinés et, en cas de besoin, des usinages par interpolation 5 axes.
Un concept de plateforme variable
En fonction des projets, les différentes possibilités d’usinage sont presque infinies. Ainsi il est possible d’effectuer des opérations de perçage et de forage de grandes dimensions de même que de multiples opérations d’usinage intérieur sur les pièces à usiner. L’aire de travail complètement fermée est un facteur de sécurité pour les projections de copeaux, et permet également l’utilisation de technologies innovantes grâce à des liquides d’arrosage sous ultra-haute pression ainsi que l’utilisation de process de perçage profond avec de très grands volumes de liquide d’arrosage. En outre, le nouveau concept de plateforme variable breveté offre à l’utilisateur de la machine le meilleur accès possible à la pièce usinée, quels que soient ses contours extérieurs. Des magasins d’outils à disques, accessibles par l’avant, avec 90 places, peuvent recevoir des outils pouvant atteindre une longueur de 1 000 mm et un poids de 40 kg. L’utilisateur de la machine peut gérer les besoins en outils facilement grâce à la fenêtre particulièrement grande. Cependant, il n’y a pratiquement pas de limites aux souhaits des clients en matière de versions de magasins et un magasin à chaînes de 200 places est également disponible en option. De plus, si les dimensions du magasin standard ne sont plus suffisantes, il existe des options automatisées possédant une propre interface lourde pour des outils jusqu’à 3 m de long. D’autre part, il est possible, de fournir un chariot particulièrement stable pour des usinages intérieurs difficiles tout comme pour l’attachement de groupes spéciaux, comme par exemple des rotors rainurés ou des groupes de fraises à disques.
Intégration de la fabrication additive
WFL ne passe pas non plus à côté du thème de la fabrication additive. L’intégration d’un laser 10 kW haute puissance permet non seulement la fusion de matériaux industriels mais également la trempe précise et sans déformation de surfaces à usure rapide. Lors de la fusion de matière, il est non seulement possible de suivre des trajectoires rectilignes avec un taux élevé de rechargement mais également de réaliser pratiquement toutes les formes géométriques par l’utilisation des nombreux axes numériques du Millturn. Il est ainsi possible de produire efficacement des canaux de refroidissement ou des brides hydrauliques courbées. La technologie laser représente une nouvelle étape dans l’évolution de la machine d’usinage complet, car les opérations nécessitant auparavant un serrage et des travaux externes peuvent maintenant être réalisées dans le cadre de l’usinage complet, ce qui présente non seulement des avantages au niveau du temps de cycle et du pilotage du process mais apporte également des améliorations notables en termes de qualité de la pièce usinée tout en permettant de réduire considérablement le temps de montage. La gamme WFL Millturn est représentée en France par la société Mehrtech.
à propos de WFL Millturn Technologies
les plus lus
à lire aussi
Les nouveaux produits
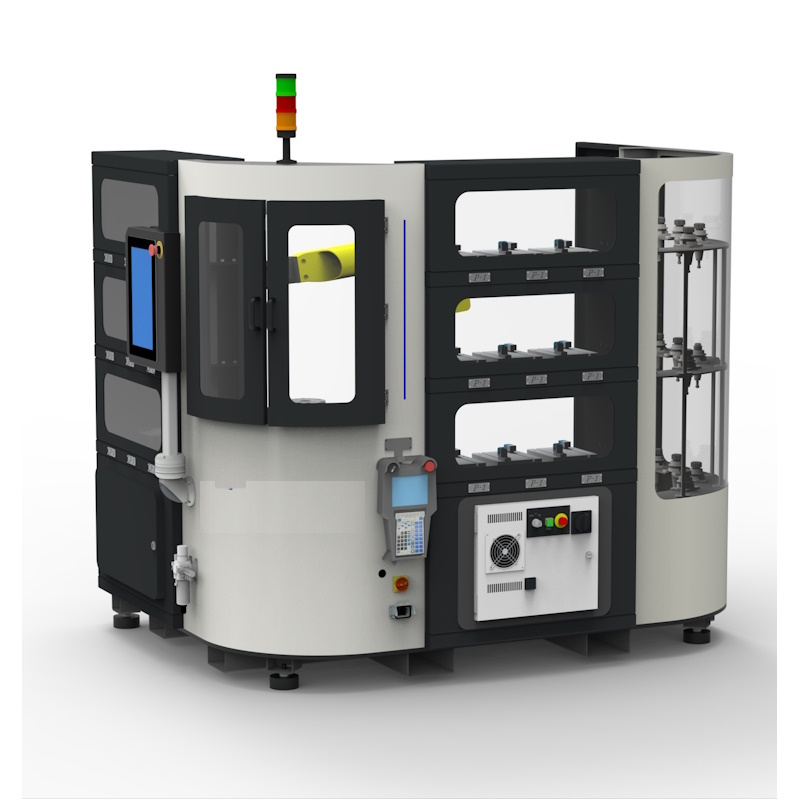
Robotique FANUC pour l'usinage pièces unitaires sur plateforme CUBEBOX
PALETTE, la station robotisée pour les palettes et les systèmes de serrage sur centres d'usinage