De l’eau claire à l’aide de centrifugeuses
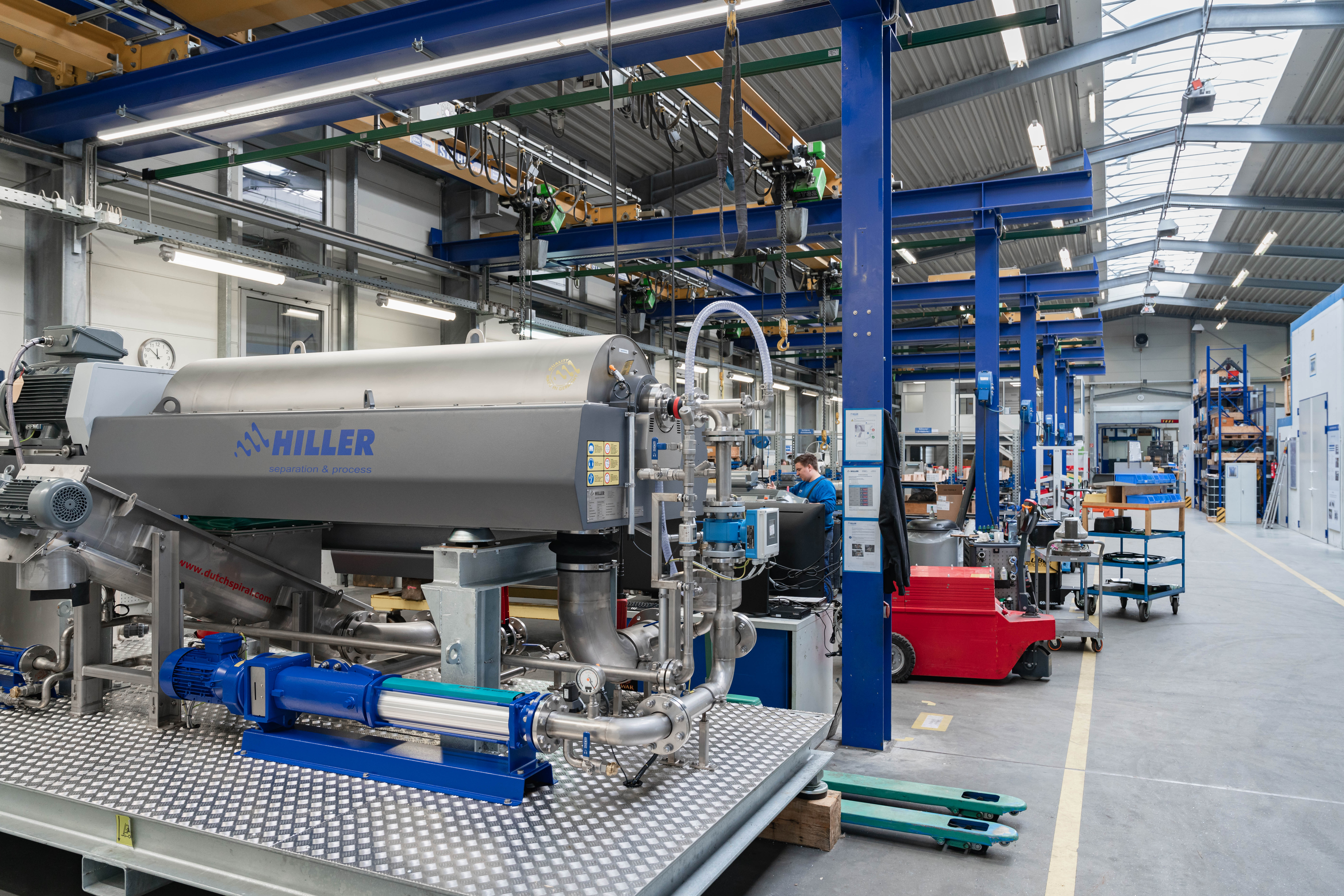
La technologie des décanteurs est un procédé de séparation des liquides et des solides. Une société allemande se concentre depuis plus de 50 ans sur le développement et la production de décanteurs centrifuges et utilise son expérience pour accompagner les industriels dans de nombreux secteurs.
Si l’on pense aux jus de fruits et de légumes, à l’huile d’olive, à la transformation du poisson, aux produits laitiers, aux déchets de cuisine, au traitement des boues d’épuration, à la récolte des algues, à la préparation de l’huile ou même aux extractions de végétaux, on ne saurait pas, à première vue, ce qui relie ces domaines. Pourtant, c’est précisément là que Hiller intervient. Les décanteurs Hiller assurent par exemple la séparation du lait et de la crème dans l’industrie alimentaire ou sont utilisés pour l’extraction de l’huile d’olive. On peut par exemple estimer que plus de 80 % de l’huile d’olive espagnole passe par un décanteur Hiller. Une autre application intéressante se trouve dans l’industrie chimique, où les décanteurs servent à séparer les solvants ou à traiter les eaux usées. Le domaine le plus important et le plus durable est celui du traitement des eaux usées. Les décanteurs sont utilisés ici pour séparer les solides et les liquides dans les stations d’épuration. Les eaux usées produites sont nettoyées à l’aide de décanteurs afin de pouvoir les rejeter dans les eaux. Un sujet dont nous sommes à peine conscients, mais qui nous concerne tous.
Focus sur la séparation solide-liquide
Quelle est la nature d’un décanteur et que se cache-t-il derrière cette technologie phénoménale ? Un décanteur se compose d’un corps cylindrique avec un tambour rotatif à l’intérieur. Le tambour est divisé en deux sections par une paroi de séparation. L’une des sections est alimentée par le liquide à séparer, tandis que l’autre est utilisée pour évacuer le produit final et les solides issus de la séparation. Lorsque le tambour tourne, il se produit une force centrifuge qui pousse les solides vers l’extérieur. En même temps, les liquides les plus lourds, comme l’eau, descendent vers la paroi extérieure du tambour et y sont évacués. Les liquides plus légers, comme l’huile, flottent à la surface du liquide plus lourd et sont également séparés.
La technologie des décanteurs présente l’avantage de permettre une séparation très efficace des liquides et des solides tout en consommant très peu d’énergie. Pour fabriquer ses décanteurs, Hiller mise sur la production interne et fabrique la plupart des composants des décanteurs sur son site de Vilsbiburg.
Introduction de l’usinage complet
La société Hiller GmbH usine les composants les plus divers des décanteurs centrifuges dans des centres de tournage-fraisage MillTurn du fabricant WFL. Le cœur de la décanteuse est le rotor, qui est entièrement usiné sur les machines multi-talents de WFL et qui se compose d’une vis sans fin, d’un tambour et d’une unité d’entraînement. Avec la nouvelle M50 MillTurn d’une largeur de pointe de 2000 mm, des pièces supplémentaires, qui étaient jusqu’à présent achetées, sont désormais fabriquées. La stratégie d’internalisation est une priorité pour Hiller GmbH. Face aux difficultés de livraison qui ont été un thème récurrent ces derniers temps, Hiller mise sur la stratégie de l’indépendance.
Stefan Brauner, responsable de la production, donne un aperçu de la fabrication : « Avec le nouveau Tour-Fraiseur Multifonctions WFL, on essaie de produire des lots plus grands ou de les exploiter de manière optimale. Avant l’utilisation de l’usinage complet, le parc de machines était plus important. Plusieurs centres d’usinage ont été échangés et remplacés par le nouveau WFL. Le grand avantage réside dans la simplification du processus de fabrication. Auparavant, le processus était plus long : sur une machine, on tournait, puis on fraisait, parfois on tournait à nouveau. Selon les besoins, les différentes étapes de fabrication étaient réparties sur différents centres d’usinage. Maintenant, tout fonctionne en un seul, on n’a même plus besoin de changer de serrage ».
Les collaborateurs de la production sont également fans de ces machines. Avec le trio M50, M80 et M120, on dispose d’un très bon équipement de production qui peut gérer différentes tailles de pièces. Ainsi, les mêmes mandrins sont utilisés sur les plus grandes WFL et on y produit principalement des pièces telles que des tambours coniques, des tambours cylindriques, des corps de vis et des parois frontales, etc. Concernant la M50, on produit actuellement des pièces de transmission.
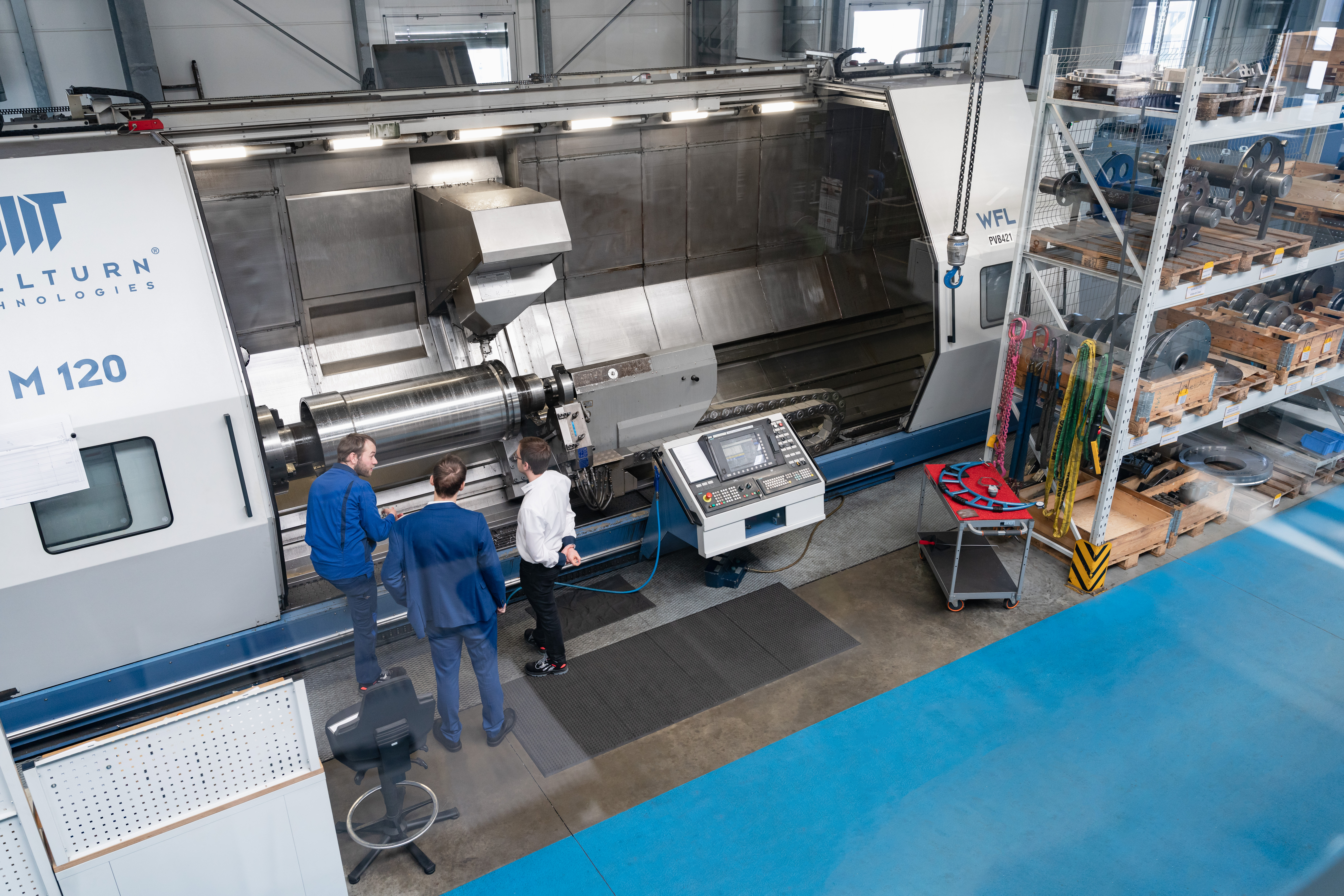
Fabrication de rotors de centrifugeuses.
Sur les grandes machines, M80 et M120, on réalise des lots plus petits, entre cinq et dix pièces. Sur la nouvelle M50, on fabrique en revanche 20 à 50 pièces en deux équipes. Les avantages de l’usinage complet sont évidents : le processus de fabrication d’une pièce se déroule sur une seule machine, contrôle qualité compris. La possibilité d’intégrer un grand nombre d’outils dans la machine parle d’elle-même. Les temps d’équipement réduits et les temps de passage généralement faibles font de l’usinage complet une solution incontournable pour nous.
Andreas Lehner, directeur commercial de WFL, ajoute : « Parmi les USP de nos machines figure la très grande stabilité due au concept de banc incliné. Les machines présentent des distances d’action courtes entre le point d’enlèvement de copeaux et les guides. Une efficacité maximale lors de l’enlèvement des copeaux ainsi qu’une précision maximale lors de la finition sont ainsi garanties ».
Qualité et fiabilité
Les critères les plus importants lors de l’achat des centres d’usinage complets étaient la sécurité des processus, la disponibilité du service et surtout la grande qualité des machines. Comme un M80 et un M120 étaient déjà en service depuis un certain temps, on savait que le service était impeccable. Cela a également été un point décisif pour l’achat d’une autre Millturn.
« Une équipe compétente, qui peut déjà aider au téléphone en cas de problème, ainsi que la télémaintenance sont des solutions de pointe. L’utilisateur peut établir une connexion sécurisée avec WFL au moyen d’un code pin et en un clin d’œil, un technicien du service de WFL se connecte à la commande pour identifier le problème ou établir un diagnostic. La proximité et les temps de réaction rapides sont tout simplement top », conclut Stefan Brauner.
Andreas Lehner ajoute : « Il n’est pas seulement important que quelqu’un soit sur place le plus rapidement possible en cas de service, afin de résoudre rapidement le problème. Ce qui est particulièrement important pour nos clients, c’est le temps nécessaire à la reprise de la production. Chacun de nos collaborateurs du service après-vente est formé sur tous les types de machines et peut ainsi assister au mieux le client sur place ».
Comme Hiller attache une grande importance à la qualité de ses produits, une conception parfaitement adaptée de la technologie était un facteur décisif. Stefan Geiger, programmateur CN, explique que le processus d’usinage a été développé en amont avec WFL afin de pouvoir fabriquer les pièces d’engrenage demandées et en respectant les précisions requises. « L’examen préalable de la pièce a été géré de manière très précise par WFL, ce qui nous a permis d’être sûrs d’une fabrication de haute précision ».
Une diversité technologique qui compte
D’un point de vue technologique, les MillTurn sont à la pointe de ce qui se fait de mieux. Actuellement, on essaie d’intégrer le processus technologique du mortaisage. Il serait envisagé de traiter les dentures intérieures des pièces d’engrenage également avec les centres d’usinage complets. Les dentures extérieures ont déjà été réalisées avec succès avec les cycles technologiques propres à WFL. Les temps d’usinage des différentes pièces varient en fonction de la taille de la pièce. Pour les pièces de tambour, le temps d’usinage est un peu plus long, on parle alors de temps de marche de 1,5 à 3,5 heures. La plupart des pièces à usiner sont en acier inoxydable, les pièces d’engrenage sont principalement en acier. Des matériaux qui peuvent très bien être usinés avec la machine d’usinage complet WFL.
Avec iControl Advanced+, la sécurité des processus est garantie sur la M50, de sorte que la machine peut fonctionner de manière entièrement automatique. La machine permet une surveillance continue des signaux de processus sur la commande, de sorte que la moindre irrégularité peut être immédiatement détectée. Si une surcharge due à l’usure ou une rupture d’outil est détectée, la machine s’arrête automatiquement. De plus, grâce à la possibilité de mesure intégrée, les outils sont automatiquement corrigés afin de garantir un processus d’usinage parfait.
Pour la programmation, on travaille avec le système de programmation CAD/CAM TopSolid. En outre, Hiller mise désormais davantage sur le logiciel de simulation et de programmation CrashGuard Studio de WFL, qui est utilisé pour l’optimisation finale des programmes.
Le développement durable, une priorité
Chez Hiller, on fabrique des produits qui aident l’environnement à se régénérer. Le technicien en décantation contribue à rendre les eaux polluées à nouveau potables. Dans le secteur alimentaire, les aliments peuvent être conservés plus longtemps, ce qui contribue à réduire les pertes alimentaires et à améliorer l’efficacité des ressources. En résumé, l’utilisation de décanteurs permet de séparer efficacement les matières solides des matières liquides en vue de leur réutilisation ou de leur élimination. Cela contribue généralement à minimiser les déchets et à préserver les ressources. Les machines WFL hautement efficaces s’inscrivent donc parfaitement dans la philosophie de développement durable de Hiller.
à propos de WFL Millturn Technologies
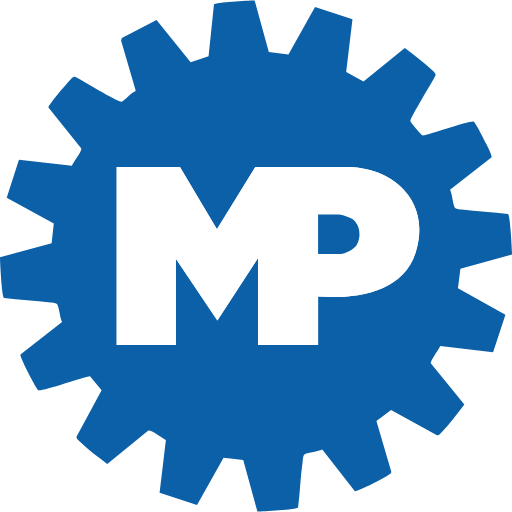
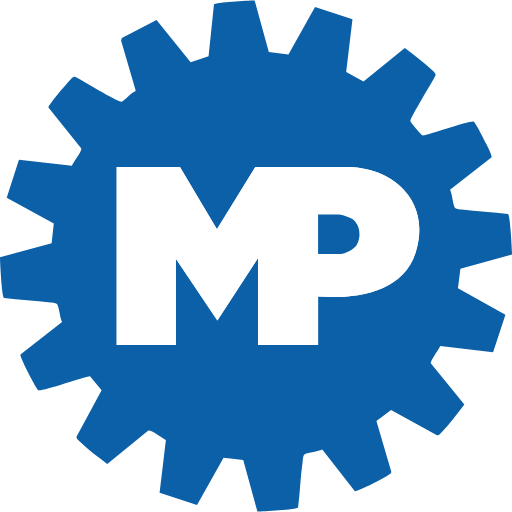
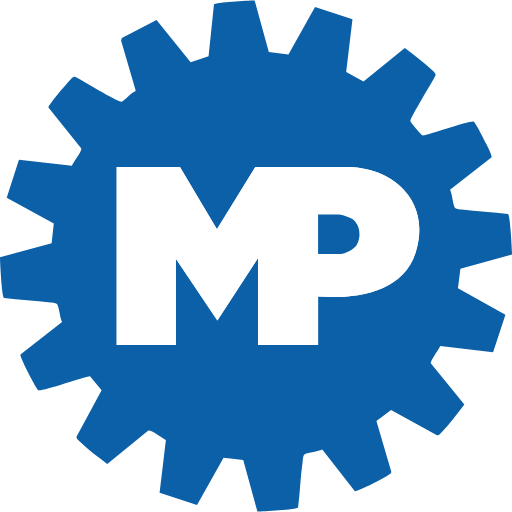
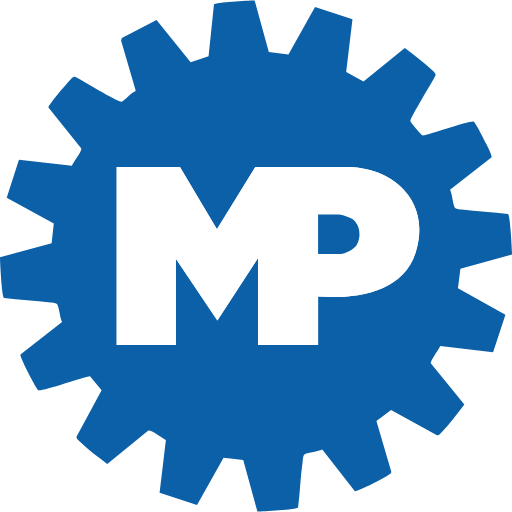
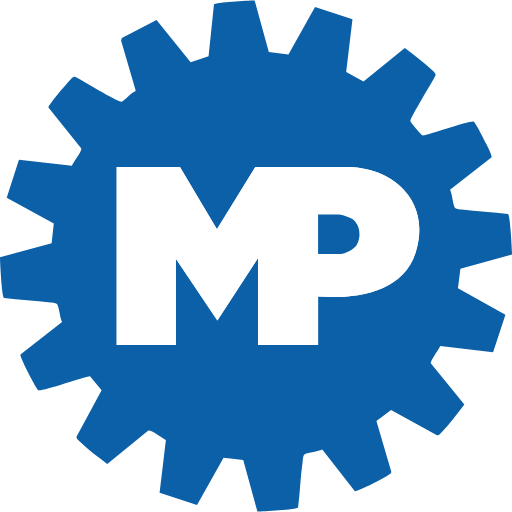