L’aluminium, un métal durable pour l’industrie de demain
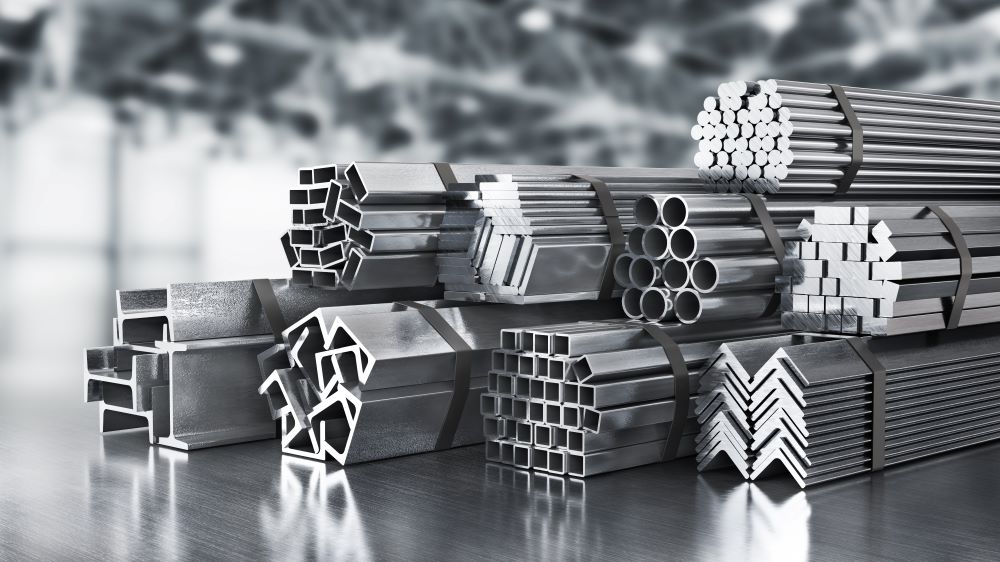
Avec ses propriétés exceptionnelles et son potentiel de recyclage infini, ce métal léger est le deuxième le plus utilisé dans le monde. De l’extraction à la production, découvrez les étapes cruciales de sa transformation et comment l’industrie cherche à en réduire l’impact environnemental.
Alexis Noyer est expert de l’industrie du recyclage de l’aluminium sur le marché européen et mondial. Ce fin connaisseur de l’économie circulaire maîtrise la production d’aluminium primaire, de la gestion des déchets jusqu’à sa refusion, en passant par le traitement de la matière. Il a été directeur commercial d’une société spécialisée dans le broyage de véhicules hors d’usage et cofondateur d’un site industriel de traitement de déchets d’aluminium. Cet ancien directeur d’une affinerie d’aluminium explique comment produit-on de l’aluminium en France : de l’utilisation de la bauxite pour obtenir de l’alumine, à sa transformation pour en faire de l’aluminium, sous forme de plaques, lingots ou bien de barres. Interview.
Pourquoi l’industrie métallurgique est une grande consommatrice d’aluminium ?
Parce qu’il est très polyvalent et, pour cette raison, il est actuellement le deuxième métal le plus consommé après l’acier. C’est l’un des métaux les plus utilisés dans l’ingénierie, car il présente un meilleur rapport résistance/poids que l’acier. De plus, l’aluminium est recyclable à 100 % et à l’infini, sans dégradation de ses propriétés. C’est donc une matière respectueuse de l’environnement.
On différencie l’aluminium primaire, qui est produit à base de minerai, de l’aluminium secondaire, issu du recyclage. Comment produit-on de l’aluminium primaire ?
Sa production s’effectue en plusieurs étapes. Tout d’abord, la bauxite est extraite et traitée pour obtenir de l’alumine. La bauxite est une roche sédimentaire constituant le minerai d’oxyde d’aluminium, environ 50 %, souvent appelé alumine (Al2O3). Ensuite, l’alumine est transformée en aluminium par électrolyse. Enfin, l’aluminium obtenu est affiné pour répondre aux normes de qualité spécifiques.
Avant de poursuivre, dites-nous par quel processus peut-on extraire l’alumine de la bauxite ?
Par un processus chimique qu’on appelle la Bayerisation, parce que mis au point par le chimiste Karl-Josef Bayer au début du XXe siècle. La bauxite est broyée et mélangée à de la soude caustique (hydroxyde de sodium) dans des autoclaves sous pression. Cela provoque la dissolution de l’alumine contenue dans la bauxite sous forme de solution de sulfate d’aluminium. Celle-ci est ensuite traitée pour précipiter l’alumine. Cela se fait généralement en refroidissant la solution, ce qui provoque la cristallisation de l’alumine. Cristaux qui sont séparés du reste de la solution à l’aide de filtres, avant d’être lavés pour éliminer les impuretés. Ensuite, ces cristaux d’alumine sont chauffés pour produire de l’alumine pure ou oxyde d’aluminium Al2O3. L’alumine ainsi obtenue est ensuite utilisée comme matière première dans le processus d’électrolyse pour produire de l’aluminium primaire.
Justement, décrivez-nous cette étape primordiale qu’est l’électrolyse…
Une fois transformée en cryolithe, un composé chimique de fluorure double de sodium et d’aluminium (3NaF,AlF3) qui permet de réduire sa température de fusion, l’alumine dissoute est soumise à un courant électrique, on la fait fondre à des températures autour de 950 degrés Celsius. L’alumine dissoute est soumise à un courant électrique, par un processus électrolytique, qui dissocie l’alumine en aluminium liquide et en oxygène gazeux. Une anode est placée en haut d’un creuset où s’effectue l’électrolyse. L’oxygène peut ainsi se dégager sous forme de CO2 gazeux, après avoir brûlé le carbone qui constitue l’anode. Quant à la cathode, elle est située au fond du creuset, où l’aluminium plus lourd que le bain se dépose et reste sous forme d’une couche liquide.
Et que se passe-t-il ensuite ?
L’aluminium liquide est aspiré puis refroidi pour être coulé afin de se solidifier sous forme de plaques, de lingots ou d’autres formes, selon les besoins.
Et produit-on toujours de l’aluminium primaire en France ?
Bien sûr, la France a gardé une capacité industrielle de fabrication d’aluminium primaire avec ses deux usines d’électrolyse et fonderies d’aluminium primaire que sont Aluminium Dunkerque et Trimet Saint-Jean-de-Maurienne. La première est adossée à une centrale nucléaire, tandis que la seconde à un barrage hydroélectrique.
Et pour quel volume ?
Selon les chiffres de 2019, on en produit 420 000 tonnes par an.
Nous l’avons vu dans votre description, ce processus consomme une quantité significative d’énergie, principalement en raison de l’étape d’électrolyse qui requiert une température élevée et une alimentation électrique importante…
C’est pourquoi l’industrie de l’aluminium représente environ 6 % de la consommation électrique de l’industrie française.
Mais cherche-t-elle à réduire son empreinte carbone ?
Parce que cette intensité énergétique est élevée, elle cherche constamment des moyens d’améliorer l’efficacité énergétique de la production, notamment par le biais de technologies plus avancées et de pratiques durables.
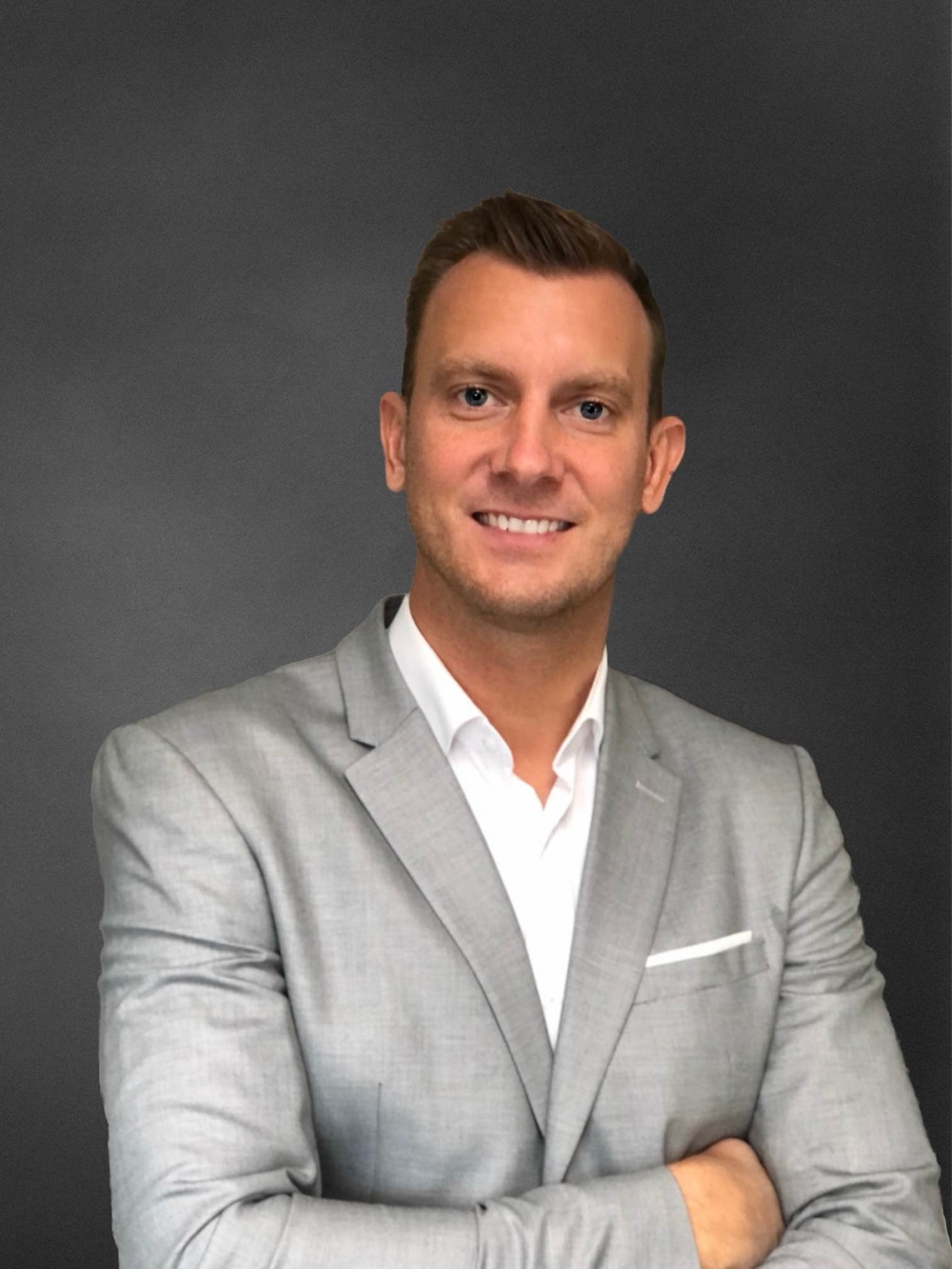
Alexis Noyer, expert de l’industrie du recyclage de l’aluminium.
à propos de fabrication
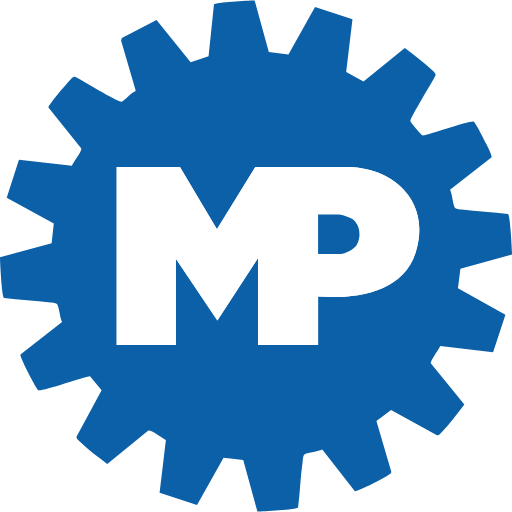
les plus lus
à lire aussi
Les nouveaux produits

Kit de composants de serrage pour la fixation d’appareils de mesure tridimensionnelle, principe de la colonne