L’usinage grande vitesse, une technologie d’avenir
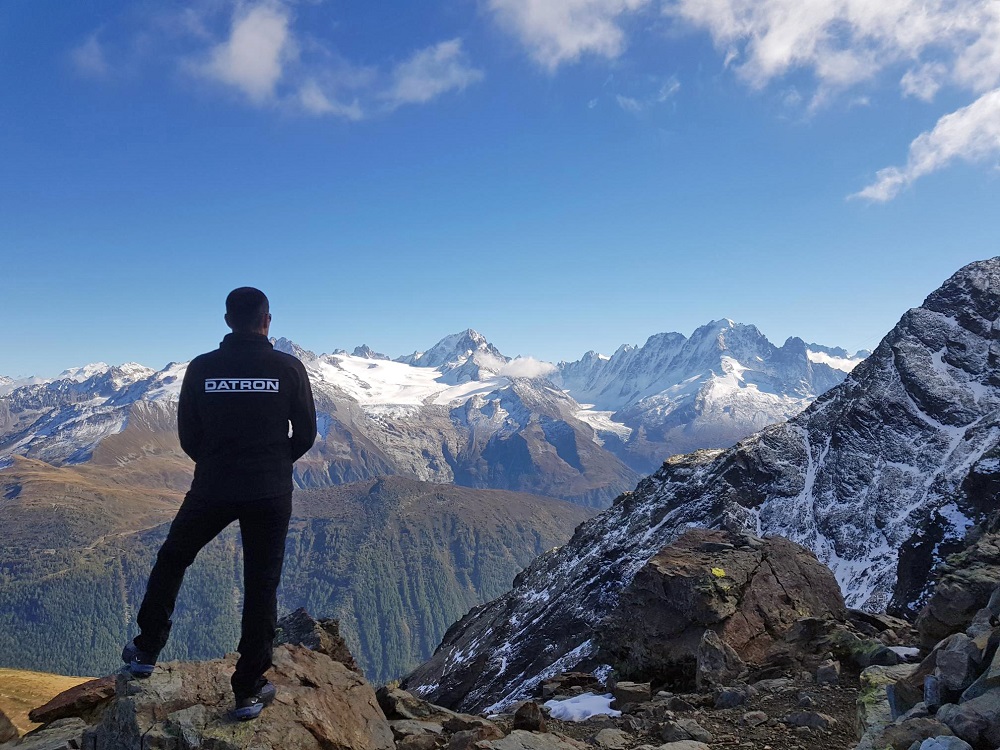
Pour beaucoup, le terme d’usinage a longtemps eu une connotation péjorative. Il évoquait des images d’ateliers sales, bruyants, occupés par des machines énormes, compliquées à utiliser, dégoulinantes d’huile… Mais depuis quelques années l’usinage grande vitesse (UGV) a fait son apparition. Derrière ce concept ne se cache pas une action « marketing » mais une véritable révolution technologique.
Chez Datron, « l’UGV, on ne connait que ça… et nous croyons que cette vision novatrice de l’usinage, gage de rentabilité et d’une gestion plus rationalisée des ressources, a beaucoup à nous offrir », affirme le constructeur allemand de machines-outils, pour qui l’usinage grande vitesse est une « seconde nature ».
La société, fondée en 1959, est basée à Darmstat, en Allemagne. A l’origine fabricant de composants pour l’électronique, Datron développe dans les années 1980, une nouvelle génération de centres d’usinage innovants orientés UGV.
Aujourd’hui encore, Datron collabore sur de nombreux projets de recherche avec « the Machinery University » de l’université de Darmstadt pour développer cette technologie d’usinage toujours plus respectueuse des ressources naturelles et de l’environnement, tout en offrant à ses clients une productivité et une qualité accrues.
Mais alors l’UGV, c’est quoi au juste ? L’usinage grande vitesse est une opération d’enlèvement de matière à des vitesses de coupe très élevées. On résume souvent l’UGV à une méthode d’usinage qui favorise l’évacuation de la chaleur émise lors de la coupe vers le copeau plutôt que la matière usinée. C’est vrai ! Mais bien restrictif. Grâce aux vitesses de coupe élevées, c’est l’ensemble des phénomènes intervenant entre la pièce, l’outil et le copeau qui différent de ceux observés en usinage conventionnel.
Si vous avez vu tourner des centres UGV et conventionnels, vous avez constaté une différence majeure d’aspect des copeaux. A faible vitesse de coupe le copeau est continu et se forme par un phénomène mécanique de déformation et arrachement. À vitesses de coupe élevée se forment de petits copeaux fins qui semblent générés par une rupture « instantanée » du matériau, plus que par une déformation et un cisaillement, d’où un copeau fractionné.
Pourquoi ces différences entre usinage et UGV ? La puissance absorbée par la coupe résulte principalement de trois composantes : puissance due aux frottements, puissance nécessaire à la déformation plastique du matériau et puissance nécessaire au cisaillement (rupture). C’est sur l’équilibre entre ces trois composantes que diffèrent totalement usinage conventionnel et UGV.
En usinage conventionnel, le processus de formation du copeau est basé sur des déformations plastiques. Ce mécanisme consomme du couple et tend à « endommager » la matière, en créant, par exemple, des amorces de rupture, en la déformant ou laissant des marques qui nuisent aux états de surface.
Lorsqu’on augmente la vitesse de coupe, dans un premier temps, les frottements et déformations augmentent ainsi que le dégagement de chaleur, et les conditions de coupe commencent par se dégrader.
Mais si la force nécessaire à la déformation plastique augmente initialement avec la vitesse, elle baisse avec l’augmentation de température.
En augmentant encore la vitesse de coupe, la température prend le dessus, jusqu’au moment où on assiste à un basculement instantané de l’équilibre. Les frottements, efforts de déformation et de cisaillement baissent de façon soudaine et on entre dans la zone UGV, régie principalement par des phénomènes thermiques (phénomène d’impact proche de la fusion).
La puissance consommée pour la déformation devient négligeable : l’angle de frottement baisse, les efforts de coupe diminuent ainsi que les vibrations, le copeau glisse mieux sur la face de coupe de l’outil et devient moins épais.
Et bien que des énergies thermiques plus importantes soient mises en jeu, les échanges entre outils, copeaux et pièce n’ont plus le temps d’avoir lieu. L’énergie de coupe s’évacue principalement avec les copeaux et lubrifiants : le matériau usiné ne chauffe pas ou très peu.
La matière usinée subit donc à la fois moins d’efforts mécaniques, moins de vibrations et moins d’échauffement et va être usinée moyennant un coût énergétique sensiblement réduit.
Les avantages de l’UGV pour la production
L’UGV est adaptée au prototypage, à la réalisation de préséries et à la production intensive.
- Polyvalence, usinage d’une grande variété de matériaux y compris les matériaux cassants, mous ou/et thermosensibles)
- Productivité accrue, grâce à des vitesses de coupe très supérieures, surtout pour les pièces complexes nécessitants de nombreuses opérations, parfois avec de petits diamètres d’outils
- Réduction des traitements post-usinage des pièces finies machine (micro-perçages, gravures, taraudages…) : moins de polissage… pas de lavage des pièces grâce à la micro-pulvérisation éthanol, brevetée Datron
- Très bons états de surface, car moins d’efforts mécaniques, possibilité de réaliser sur la même machine des effets de textures par gravure, et/ou des états de surface proches du miroir.
- Préservation de l’intégrité et des caractéristiques intrinsèques des matériaux usinés : pas d’amorces de rupture, pas de chauffe de la pièce donc moins de modifications structurelles
- Usinage de parois fines
- Précision en limitant les déformations dues aux efforts de coupe mécaniques ainsi que la chaleur transmise à la pièce
Une production rentable, synonyme de préservation des ressources énergétiques
A l’heure où le coût de l’énergie s’envole, la rentabilité d’une production ne s’évalue plus simplement à une ou deux secondes gagnées sur un temps d’usinage. Peut-on raisonnablement envisager d’être rentables en usinant des pièces de faibles dimensions, voir même en gravant, sur des machines aux masses embarquées énormes équipées de broches 10, 15, 20 kW…
Avec la technologie UGV, la réduction drastique des efforts mécaniques va permettre de réaliser des usinages, y compris des ébauches intensives, avec des broches haute fréquence de faible puissance et des machines moins énergivores.
L’équipe Datron a récemment réalisé une vidéo dans laquelle est comparée la consommation en énergie d’une Datron Néo lors d’une ébauche dynamique dans l’aluminium avec la consommation d’un sèche-cheveux… Devinez qui a gagné ? La Datron bien sûr ! « Nous avons réalisé des comparatifs de consommation d’énergie lors de l’usinage d’une même pièce en aluminium sur différentes machines et avons obtenu des écarts pouvant aller jusqu’à fois dix », affirme l’équipe Datron.
« Ainsi, intégrer la technologie UGV Datron c’est investir dans une production rationalisée, qualitative et rentable avec en prime la satisfaction d’agir pour l’avenir en limitant la consommation de ressources », assure le constructeur.