Quand l’art et l’usinage ne font qu’un
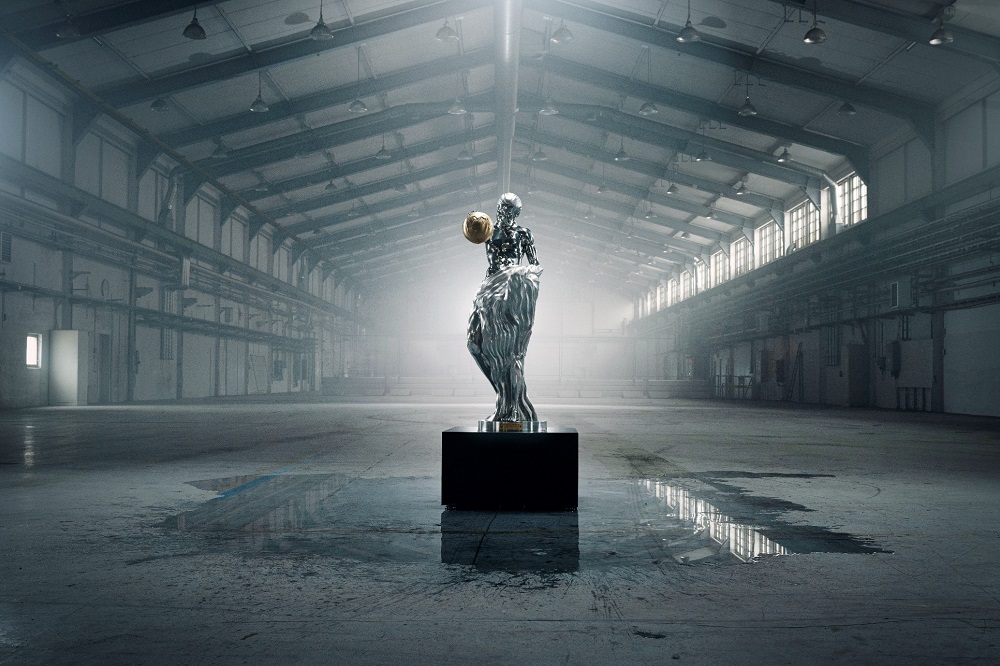
En combinant les œuvres de Michel-Ange, Rodin, Kollwitz, Takamura et Savage, des ingénieurs du groupe Sandvik sont parvenus à une prouesse technologique. Découverte.
L’art et l’industrie ne sont pas si éloignés que ça. Une prouesse technologique a permis de créer une « impossible statue », selon les mots de leurs créateurs, les Suédois Henrik Loikkanen et Jakob Pettersson, deux ingénieurs de Sandvik Coromant, dont le dessein était de concevoir une statue qui entrerait « dans l’histoire ».
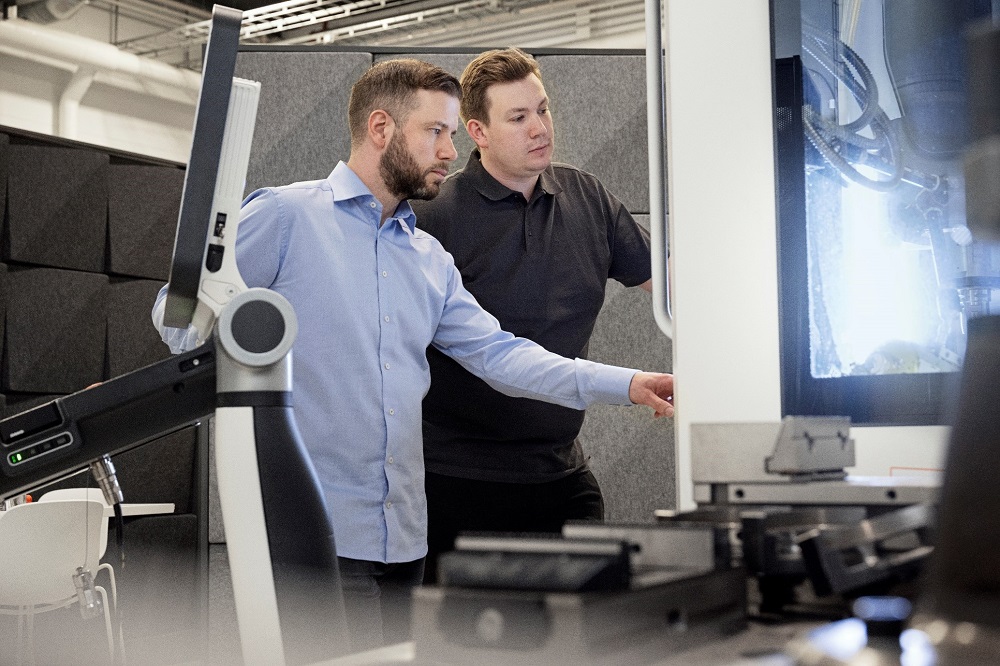
Henrik Loikkanen (à gauche) et Jakob Pettersson, les deux ingénieurs de Sandvik Coromant qui ont été chargés de transformer une idée générée par l’IA en une œuvre d’art.
Réalisée à l’aide de la modélisation par intelligence artificielle (IA) et de solutions de fabrication avancées, cette statue, dite « impossible » pèse 500 kg et mesure 150 cm. Crée à partir de bruts en acier inoxydable, elle compile les œuvres d’art des plus célèbres créateurs de l’histoire de l’art : cette sculpture « usinées » combine « les poses dynamiques de l’œuvre de Michel-Ange, la maîtrise de la musculature d’Auguste Rodin, les tonalités sombres de Käthe Kollwitz, l’influence japonaise de Kotaro Takamura et la provocation inspirante d’Augusta Savage », décrit le groupe Sandvik, à la fois producteur d’aciers et fabricants d’outils coupants.
« Affiner le corps »
Après avoir élaboré un dessin en 2D, qui réunissait les styles des cinq artistes, Sandvik a entrepris de le traduire en une image 3D complète. Au moyen « d’estimateurs de profondeur » pour construire un modèle 3D initial, « d’estimateurs de pose humaine pour affiner le corps », d’algorithmes de jeux vidéo pour générer des tissus réalistes et d’une IA spécialisée pour réintroduire les détails fins perdus au cours des étapes précédentes, le groupe mondial d’ingénierie Sandvik s’est également appuyé sur le logiciel Mastercam, pour concevoir cette statue unique, aux détails complexes et comportant plus de six millions de surfaces.
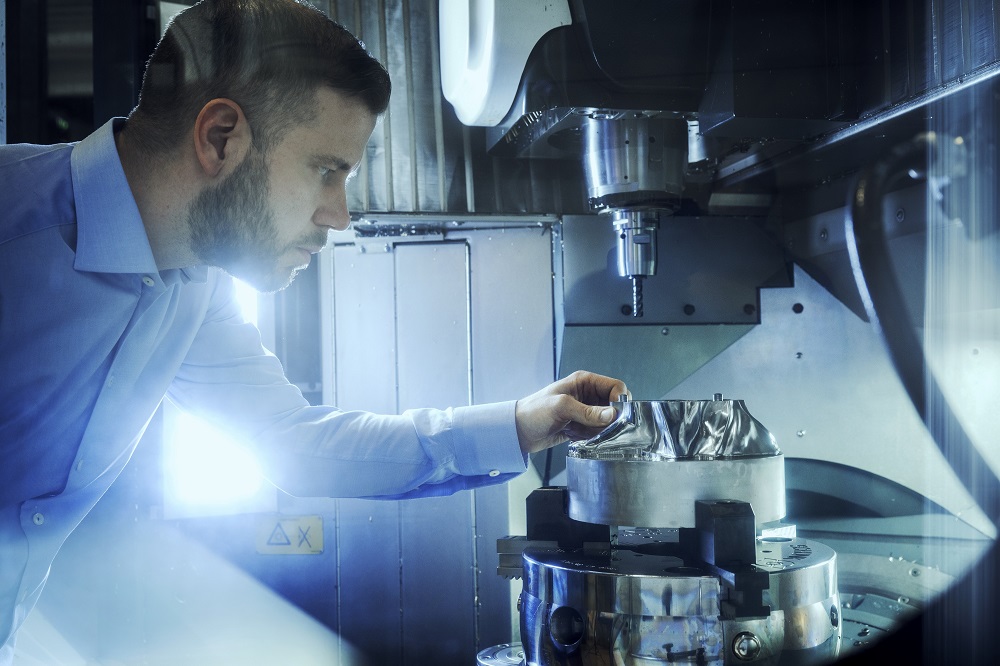
« Nous avons dû réfléchir à la méthode et au choix de l’outillage afin d’utiliser le moins d’outillage possible et de limiter ainsi les déchets. » Henrik Loikkanen, chez Sandvik Coromant.
« Il nous fallait une simulation numérique d’une précision phénoménale pour nous permettre d’usiner la statue », reconnaît Henrik Loikkanen, directeur de la technologie chez le fabricant d’outils Sandvik Coromant. Et d’expliquer que la fabrication numérique avait permis de valider à l’avance l’ensemble du process d’usinage complexe.
Statue en acier inoxydable
« Nous avons abordé la fabrication de la statue de la même manière que l’usinage de pièces complexes hautement spécialisées, comme celles que l’on trouve dans l’industrie aéronautique », poursuit-il. Le matériau choisi pour la statue, l’acier inoxydable du producteur Alleima, appartenant au groupe Sandvik, a constitué « un défi supplémentaire », indique Henrik Loikkanen, car il s’agit de matériaux ISO M, « notoirement difficiles à usiner ». Ce groupe de matériaux se caractérise par des taux d’écrouissage en coupe élevés et de faibles propriétés de rupture des copeaux pendant l’usinage. Une attention particulière doit donc être portée aux outils choisis pour l’usinage du matériau.
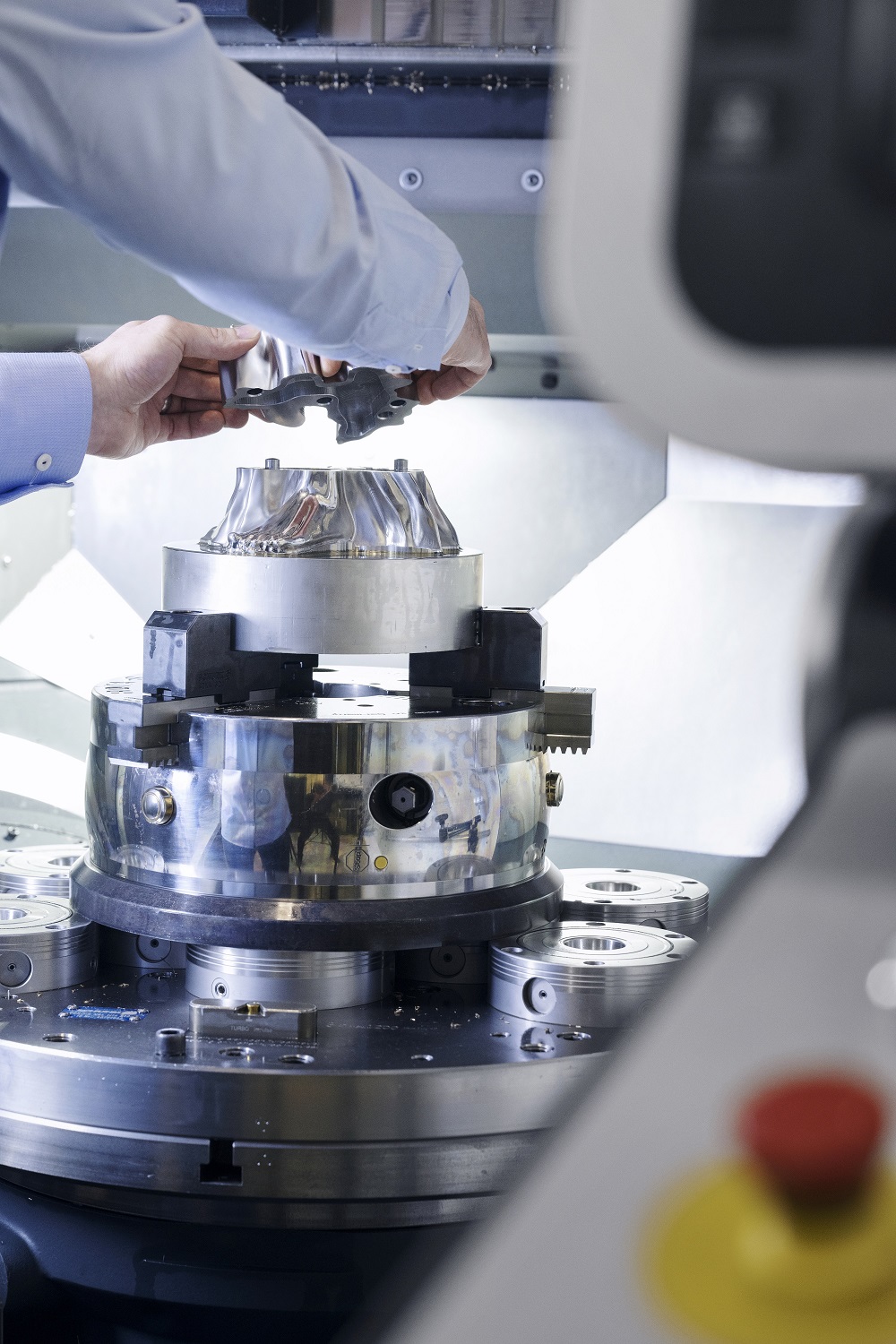
Le modèle a été divisé en 17 pièces et toutes les interfaces entre elles ont dû être modélisées avec un ajustement précis pour que les intersections soient invisibles lorsque les pièces sont assemblées.
Pour relier le bras et la tête au torse de la statue, l’interface d’outillage Coromant Capto a été utilisée, tandis que des outils rotatifs monobloc CoroMill Plura et Dura ont été employés pour la finition de toutes les surfaces. Quant à la nouvelle fraise grande avance CoroMill MH20, elle a servi à usiner la plus grande partie de l’acier inoxydable retiré de la pièce.
Choix de l’outillage
« Nous avons dû réfléchir à la méthode et au choix de l’outillage afin d’utiliser le moins d’outillage possible et de limiter ainsi les déchets », admet le cocréateur de la statue, dont son usinage brut a été réalisé avec un mélange de fraises en carbure monobloc CoroMill Plura et Dura. « Le profilage brut de la forme finale a dû être réalisé avec un outillage assez long, explique Henrik Loikkanen. Dans ce cas, une combinaison de fraises à grande avance MH20 montées sur des queues en métal lourd convenait parfaitement. »
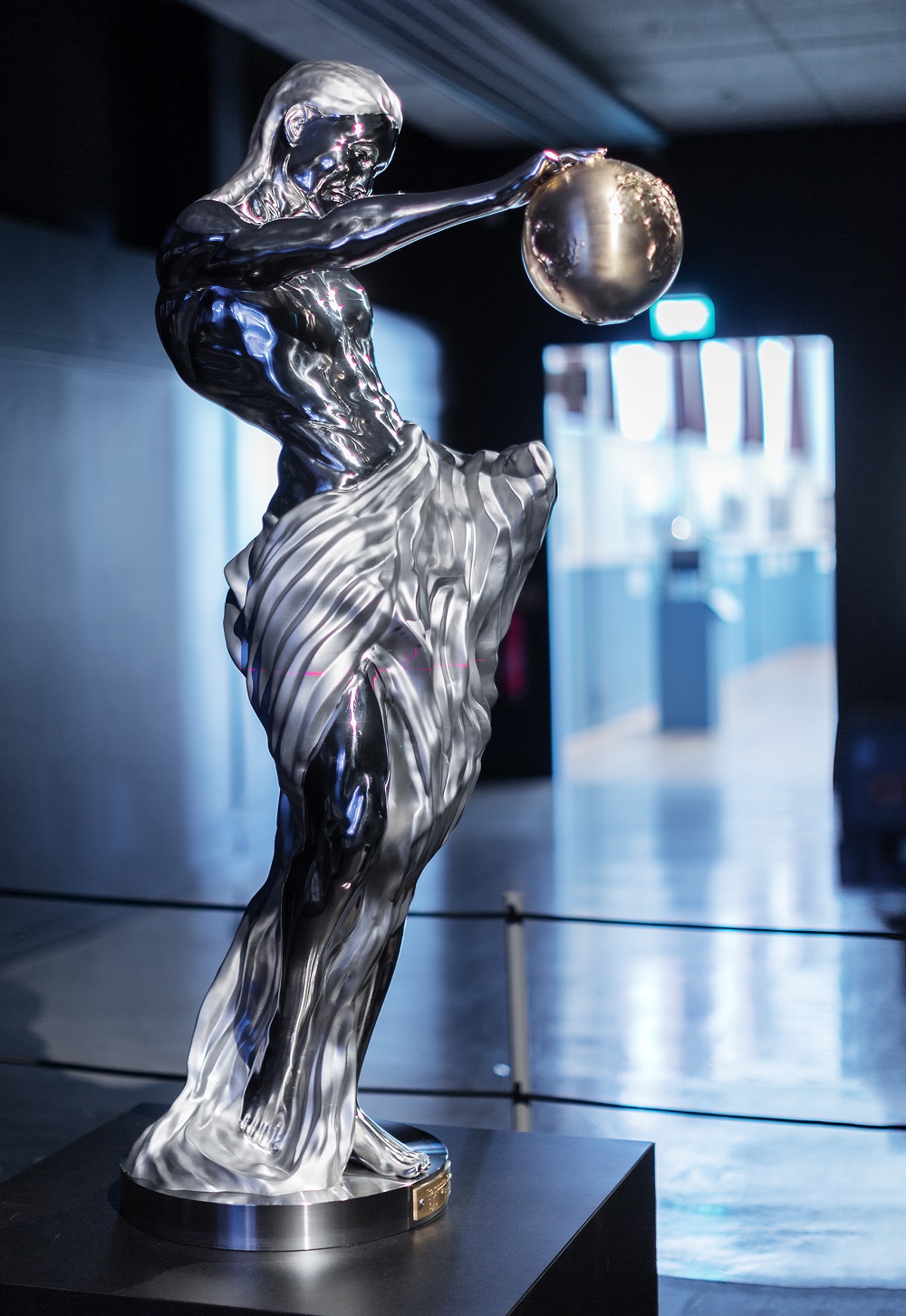
La « statue impossible » de Sandvik exposée musée national suédois de la science et de la technologie Tekniska Museet. (photo Anna Gerdén/ Tekniska Museet)
L’une des difficultés rencontrées était que le modèle 3D initial n’était pas le type de modèle avec lequel les systèmes de CAO/FAO pouvaient travailler. « Il a fallu convertir un modèle de maillage 3D, qui est essentiellement une coquille de polygones de surface couramment utilisée dans les studios d’animation 3D, en un modèle 3D solide avec densité, ce qui a été un process assez difficile, explique Henrik Loikkanen. Une fois terminé, le modèle a été divisé en 17 pièces et toutes les interfaces entre elles ont dû être modélisées avec un ajustement précis pour que les intersections soient invisibles lorsque les pièces sont assemblées. Il a fallu du temps pour que tout soit parfait. »
Autre obstacle rencontré par nos deux usineurs-sculpteurs, lors de l’ébauche : « En raison de la taille de la pièce par rapport aux machines, nous avons résolu ce problème en simulant le code NC et en identifiant toutes les zones où nous atteindrions la limite de la zone d’usinage de la machine et en modifiant la séquence FAO », précise Jakob Pettersson.
La « statue impossible » de Sandvik est visible, depuis avril, au Tekniska Museet, le musée national suédois de la science et de la technologie.