Comment donner une seconde vie aux composants de vos machines industrielles
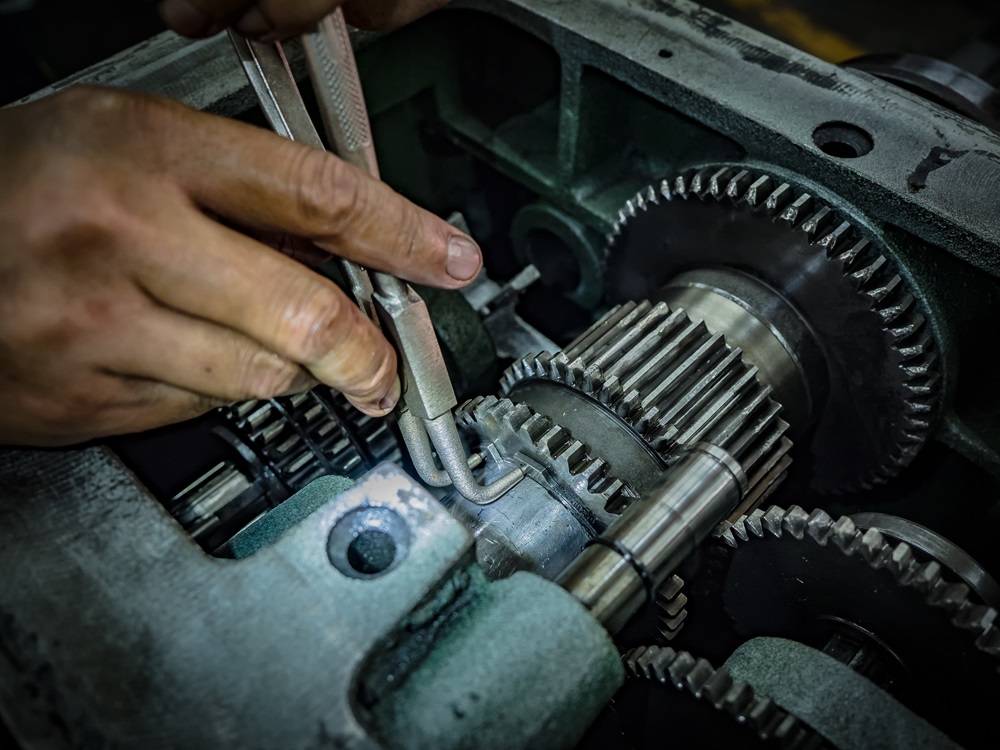
Reconditionner des équipements industriels a bien des vertus, surtout si l’entreprise est engagée dans une démarche d’économie circulaire. Un livre blanc donne plusieurs pistes sur les différentes manières de concilier performance de l’outil industriel et développement durable.
Aujourd’hui, est-il imaginable de se débarrasser des aimants permanents qui se trouvent dans les moteurs électriques, sachant que ces derniers sont fabriqués à partir de terres rares ? C’est pour accompagner les entreprises, soucieuses de leur impact environnemental, que Bosch Rexroth a édité un livre blanc sur le reconditionnement des composants de machines industrielles. Une prise de conscience qui s’est accélérée avec la récente crise sanitaire due au Covid-19, qui est venue rappeler aux entreprises qu’un « approvisionnement en matières premières ou en composants n’est jamais garanti à 100 % », souligne le spécialiste des technologies d’entraînement et de commande.
Ainsi, « face à un risque de pénurie de plus en plus probable, la réparation et le réemploi deviennent des solutions à part entière, poursuit-il. Elles valent autant pour assurer la disponibilité de l’outil de production au quotidien que pour allonger sa durée d’exploitation ».
Repenser les flux industriels
Une étude vient appuyer l’analyse de Bosch Rexroth. Celle d’Opéo Conseil, un cabinet de consultants, réalisée à la demande de l’Institut national de l’économie circulaire (Inec), montre que 85 % des industriels français considèrent l’économie circulaire comme une opportunité. Et 36 % d’entre eux ont déjà intégré la circularité dans leur stratégie d’entreprise.
Premier conseil du livre blanc : prendre exemple sur le service maintenance, où il est habituel de conserver des pièces « au cas où ». Mais il s’agit bien ici d’agir davantage en profondeur. Car il faut repenser les flux industriels : investir dans de nouvelles solutions, mettre plus de moyens organisationnels et humains pour que les processus de réparation et de reconditionnement, soient aussi faciles à gérer que la commande d’un produit neuf, avertit Bosch Rexroth. Pour s’engager sur la voie de l’économie circulaire, quand il s’agit de composants, il faut bien distinguer trois actions : la réparation, la remise à neuf et le rétrofit.
Ne pas confondre rétrofit et remise à neuf
« Utilisée en curatif, la réparation se limite au remplacement du composant défectueux, explique la division industrielle du groupe Bosch. La réparation doit utiliser des composants d’origine constructeur pour que le produit réparé soit garanti. La garantie est en général de 12 mois. » La remise à neuf, désignée également sous l’acronyme REMAN, constitue une véritable remise à neuf du produit. « À la réparation du ou des composants défectueux s’ajoutent le contrôle de l’ensemble des composants, le remplacement préventif de toutes les pièces d’usure, un lavage complet et, lorsque cela est possible, une mise à jour hardware et logicielle », détaille le document. Et de rappeler qu’une opération de REMAN peut s’effectuer en curatif comme en préventif.
Une opération à ne pas confondre avec le rétrofit. Car il s’agit bel et bien d’un « service de modernisation » qui permet de prolonger la durée de vie des machines « sans concession sur la performance, en remplaçant des produits en phase d’obsolescence par des produits de dernière génération ». Mais le rétrofit à d’autres vertus : il augmente également le niveau de sécurité et d’efficacité énergétique des machines, il peut même permettre de les rendre communicantes, rappelle Bosch Rexroth, qui conseille que le rétrofit doit être réalisé avec l’utilisateur, en mode projet, de l’analyse fonctionnelle de l’existant à la remise en route de la machine modernisée.
Un effet positif sur les émissions de gaz à effet de serre
Pour le fabricant industriel de composants, les opérations de remise à neuf et de rétrofit ont un effet positif sur les émissions de gaz à effet de serre, « et ce à deux niveaux : au niveau du produit réutilisé et au niveau de la machine ou de la ligne de production dans laquelle il est intégré ».
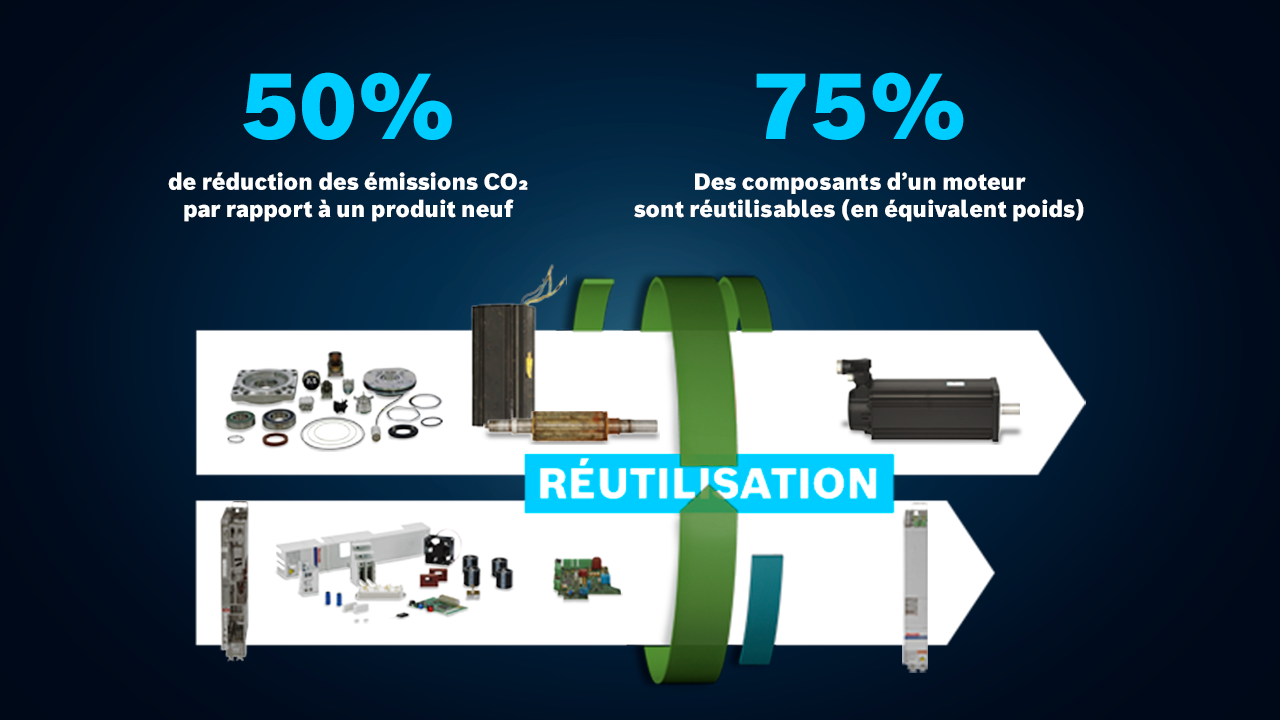
Redonner une seconde vie aux composants des machines industrielles est en adéquation avec l’économie circulaire. (infographie Bosch Rexroth)
Au niveau du produit, c’est autant d’énergie économisée, qui aurait été nécessaire à la fabrication des composants. « Une énergie consommée à la fois dans l’usine de fabrication mais aussi dans toutes les usines de la supply chain amont », souligne Bosch Rexroth, qui avance l’argument suivant : « Sachant que 90 % des produits d’automatisme peuvent avoir une seconde vie, et que le REMAN peut réduire leurs émissions de CO2 jusqu’à 50 %, l’impact global peut être très significatif. »
Quant au niveau des machines et des lignes de production, la remise à neuf des produits ou la modernisation de certaines fonctions permettent aussi de réduire la consommation d’énergie. Car les produits remis à neuf retrouveront toutes leurs performances d’origine, tandis que les produits de dernière génération bénéficieront des évolutions en matière d’efficacité énergétique.
Degré de criticité des composants
« Le rétrofit, lorsqu’il prolonge la durée de vie de la machine de 5 à 15 ans en évitant l’obsolescence, contribue aussi à réduire significativement l’impact carbone de tout ce qui sort de cette machine et de tout ce qui est produit dans la chaîne aval », explique le livre blanc, qui conclut que le rétrofit est autant bénéfique pour les émissions directes de l’industriel que pour les émissions indirectes de ses clients.
En fait, il s’agit bien de choix stratégiques à prendre en matière de gestion de l’obsolescence et de remplacement. Ceux-ci varient selon le degré de criticité des composants et des machines autant que selon le coût, les délais de livraison et les performances d’une machine neuve, rappelle le livre blanc. « Pouvoir utiliser aussi bien la réparation que le REMAN ou le rétrofit offre un meilleur degré de liberté », prévient Bosch Rexroth, pour qui, « la diversité des solutions permet de gagner du temps pour optimiser le retour sur investissement ». Car l’objectif est le suivant : que des composants critiques puissent encore être utilisés plus de 25 ans après la fin de leur commercialisation effective.
Le saviez-vous ?
- Donner une seconde vie aux composants des machines industrielles permet 50 % de réduction des émissions CO2 par rapport à un produit neuf
- 90 % des produits repris peuvent être reconditionnés
- 75 % des composants d’un moteur sont réutilisables (en équivalent poids)
Source : Bosch Rexroth