Une bibroche pour plus de compétitivité
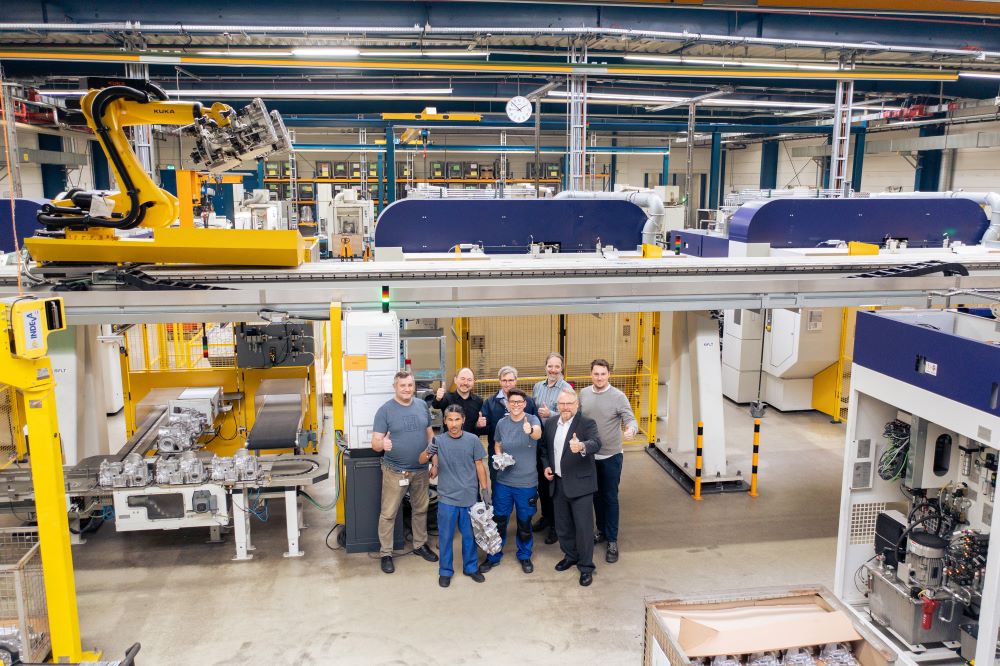
L’entreprise allemande Hengst Filtration a installé deux cellules de fabrication automatisées LiCON pour la fabrication de boîtiers de filtre pour camions et voitures. Outre plusieurs avantages économiques, le critère de la durabilité écologique a été déterminant dans le choix du constructeur de machines-outils de Laupheim.
Pour l’entreprise Hengst Filtration, située à Nordwalde, en Rhénanie-du-Nord-Westphalie (Allemagne), la durabilité joue depuis toujours un rôle décisif. En tant que fabricant leader de solutions de filtration, elle ne fabrique pas seulement des produits qui protègent l’environnement et la santé, mais son action entrepreneuriale est également orientée vers la durabilité écologique, en plus de la durabilité économique. Pour atteindre ces objectifs, Hengst recherche en permanence de nouvelles solutions.
Récemment, il s’agissait d’installer un dispositif d’usinage mécanique pour de nouveaux types de boîtiers de filtres pour camions et voitures en fonte moulée sous pression. Pour ce faire, Hengst Filtration a investi dans deux cellules de fabrication automatisées du fabricant de machines-outils LiCON, de Laupheim, dans le Bade-Wurtemberg. Le cœur des cellules de production automatisées LiCON chez Hengst Filtration est constitué de cinq bibroches de type LiFLEX II 766, qui ont été installées, clé en main, dans l’usine de Nordwalde.
Dans la plus grande cellule de fabrication, Hengst Filtration produit des boîtiers de filtres pour camions sur trois des cinq bibroches LiFLEX. Sur les deux autres bibroches LiFLEX, des boîtiers de filtre pour voitures sont fabriqués dans la petite cellule de production pour une marque allemande haut de gamme. Les centres d’usinage bibroches utilisés occupent, à rendement égal, environ 40 % de surface en moins que les monobroches utilisées jusqu’à présent. La productivité au mètre carré a donc pu être nettement augmentée. Ce n’est qu’une des raisons qui ont motivé la décision d’investissement en faveur des machines bibroches LiCON.
Rendement plus élevé par mètre carré
Dans la production Hengst, on utilisait jusqu’à présent principalement des monobroches à quatre axes. Pour l’usinage mécanique sur cinq côtés des pièces, il fallait donc jusqu’à présent au moins deux opérations d’usinage. Avec les nouveaux centres d’usinage 5 axes de LiCON, les pièces peuvent être entièrement usinées en une seule opération d’usinage. Les erreurs de changement de montage sont ainsi exclues. « Pour une évolutivité facile, il est important que les pièces soient finies dans un seul centre d’usinage. Ainsi, chaque machine supplémentaire achetée permet d’augmenter directement la capacité. Avec les centres d’usinage LiCON, nous y parvenons aussi bien avec les boîtiers de filtre pour voitures qu’avec les boîtiers de filtre pour camions », s’enthousiasme Hans-Joachim Daum, responsable du projet boîtiers de filtre pour camions, au sein du département Industrial Engineering de Hengst Filtration.
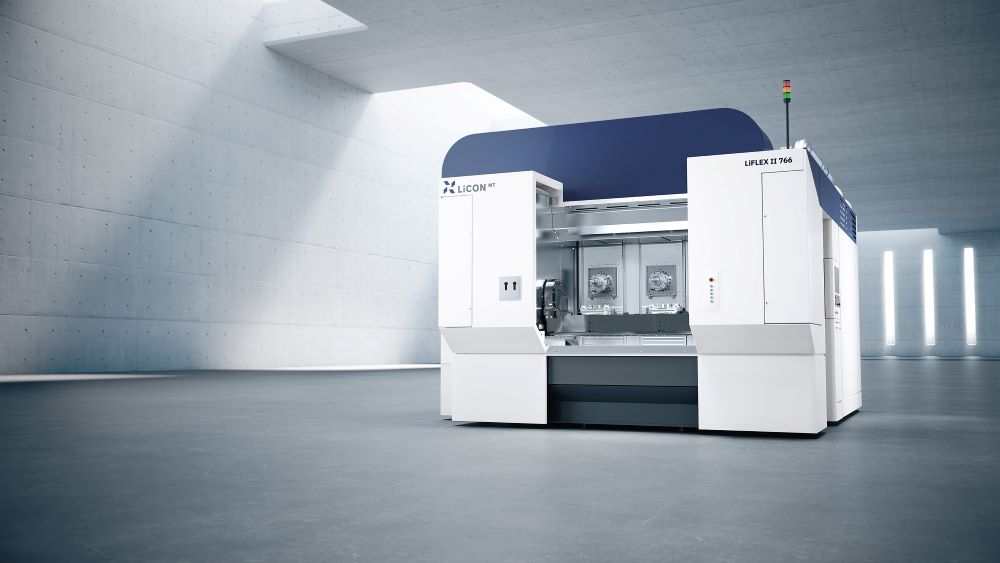
Centre d’usinage LiCON LiFLEX II 766.
Alors que jusqu’à présent, on utilisait presque exclusivement des émulsions comme lubrification de processus, on emploie désormais la lubrification par quantités minimales (MQL). Dans ce cas, un mélange d’huile et de brouillard est dosé en fonction de l’outil et amené à l’arête de coupe par des canaux de refroidissement dans l’outil. Pendant la mise en service du processus, les paramètres de dosage spécifiques à l’outil et à l’usinage sont optimisés et enregistrés dans le programme CN. On garantit ainsi que les pièces à usiner mécaniquement peuvent être retirées « quasiment à sec » du centre d’usinage. Une bibroche LiFLEX, fonctionnant avec le MQL, consomme en moyenne 15 kW. Une comparaison avec des centres d’usinage fonctionnant avec de l’émulsion montre une économie d’énergie électrique d’au moins 10 kW par heure et par centre d’usinage. Sur une durée de fonctionnement annuelle de 5 000 heures, cela représente une économie annuelle de 50 000 kWh par centre d’usinage et de 250 000 kWh pour les cinq centres d’usinage.
« Un gain de temps de cycle de 15 % »
Chez Hengst Filtration, il s’agissait d’usiner mécaniquement deux pièces de taille nettement différente, si possible avec la même technologie. Pour cette raison, le même type de machine a, certes, été choisi pour l’usinage de la grande et de la petite pièce, mais les centres d’usinage se distinguent par leurs concepts de chargement respectifs. C’est là qu’intervient le concept modulaire de LiCON. La LiFLEX II 766 est disponible dans les trois types de chargement : chargement direct, support pivotant double et changeur de palettes. Pour l’usinage de la grande pièce et le temps de cycle plus long qui en résulte, les centres d’usinage de type LiFLEX II 766 i DL B2 sont chargés directement. Pour le chargement et le déchargement, les machines sont à l’arrêt. Cette opération est toutefois si faible par rapport au temps de cycle qu’un deuxième jeu de dispositifs de montage d’usinage pour le chargement en temps masqué ne serait pas rentable. De plus, le travail de contrôle de la qualité des cavités de serrage est réduit de 50 %.
Pour le boîtier de filtre de voiture plus petit, le cas est nettement différent. Marco Gerhard, du département Industrial Engineering de Hengst Filtration, explique son projet : « En raison du plus petit cubage du boîtier de filtre de voiture, le temps de cycle est nettement plus court que pour le boîtier de filtre de camion, de sorte qu’un chargement en temps masqué représente ici la variante la plus économique. C’est pourquoi le changeur de palettes a été ici utilisé. Dans la machine, il a même été possible d’utiliser des dispositifs de serrage pour deux pièces à la fois. Deux boîtiers de filtre sont usinés par broche, donc quatre à chaque cycle dans le bibroche. Cela a permis un gain de temps de cycle de 15 %. »
Chargement par le haut de la machine
Pour l’usinage mécanique des grandes pièces, trois centres d’usinage sont utilisés en tout. Ceux-ci sont chargés et déchargés « par le haut » par un robot se déplaçant sur un pont. La pince quadruple, développée à cet effet par LiCON, dotée d’une technique de serrage flexible pour compenser les variations de la fonte brute, permet de saisir simultanément deux pièces brutes et deux pièces finies. Les pièces sont ainsi positionnées avec précision dans les dispositifs de montage d’usinage. L’usinage mécanique des petites pièces est assuré par deux centres d’usinage se faisant face, qui sont chargés et déchargés par un robot fixe. Dans les deux cellules de production, les pièces brutes sont mises à disposition par l’ouvrier sur des bandes. Les tailles de tampons choisies à chaque fois permettent un passage en pause sans intervention humaine. « La flexibilité est importante pour nous. C’est pourquoi nous voulions un accès libre pour un chargement manuel. Cela nous permet aussi de fabriquer une fois un petit lot d’un ancien type sur l’une des trois machines bibroches à haut rendement. Pour cela, le concept avec un robot se déplaçant sur le pont est idéal », explique le directeur de l’usine, Michael Cedrola, pour justifier le choix de ce concept.
à propos de fabrication
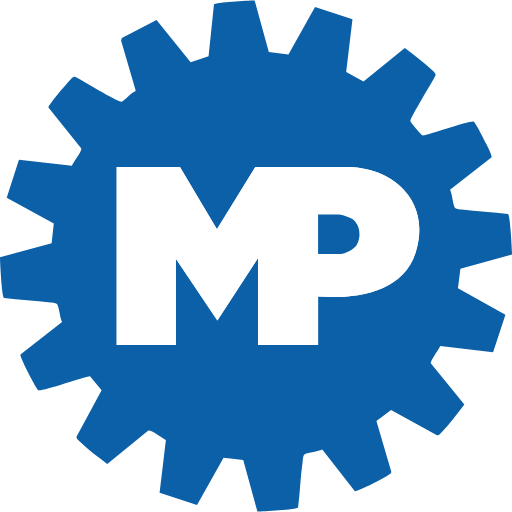