Une machine pour usiner plus rapidement les galettes SiC

Ce matériau utilisé pour la production des semi-conducteurs est particulièrement délicat à usiner en raison de sa dureté élevée. Le fabricant Usach a conçu une machine qui regroupe, automatise et optimise toutes les étapes du processus de production.
Alors que la fabrication de galettes SiC (carbure de silicium) pour la production de puces est un marché en pleine croissance, un constructeur de machines propose un modèle spécialement dédié pour la production des ces galettes, particulièrement délicates à usiner.
En effet, le matériau est produit sous forme de monocristal à partir d’une phase gazeuse à environ 2 400°C dans des fours spéciaux. Au cours d’un processus de deux semaines, ce que l’on appelle la boule croît et doit ensuite être usinée pour obtenir une ébauche de plaquette, appelé le palet. En raison de la dureté élevée du SiC, le meulage est la méthode de fabrication la plus productive.
Sauf que jusqu’à présent, le traitement ultérieur d’une boule pour en faire un palet, à partir duquel les tranches seront découpées, comprenait plusieurs étapes de processus individuelles, dont certaines nécessitaient un travail manuel considérable. Le coût des tranches traitées dépendait fortement du nombre et de la complexité de ces étapes.
Machine automatisée tout-en-un
Le fabricant américain de machines spéciales Usach s’est penché sur cette problématique et a développé avec son modèle BoulePro 200AX, un concept de machine qui « regroupe, automatise et optimise toutes les étapes du processus de production du palet », affirme cette filiale du groupe Hardinge, spécialisée dans la fabrication de rectifieuses sur mesure pour les matériaux particulièrement difficiles à usiner. Avec cette machine automatisée tout-en-un à 5 axes, la pièce peut ainsi être orientée et usinée selon les spécifications souhaitées.
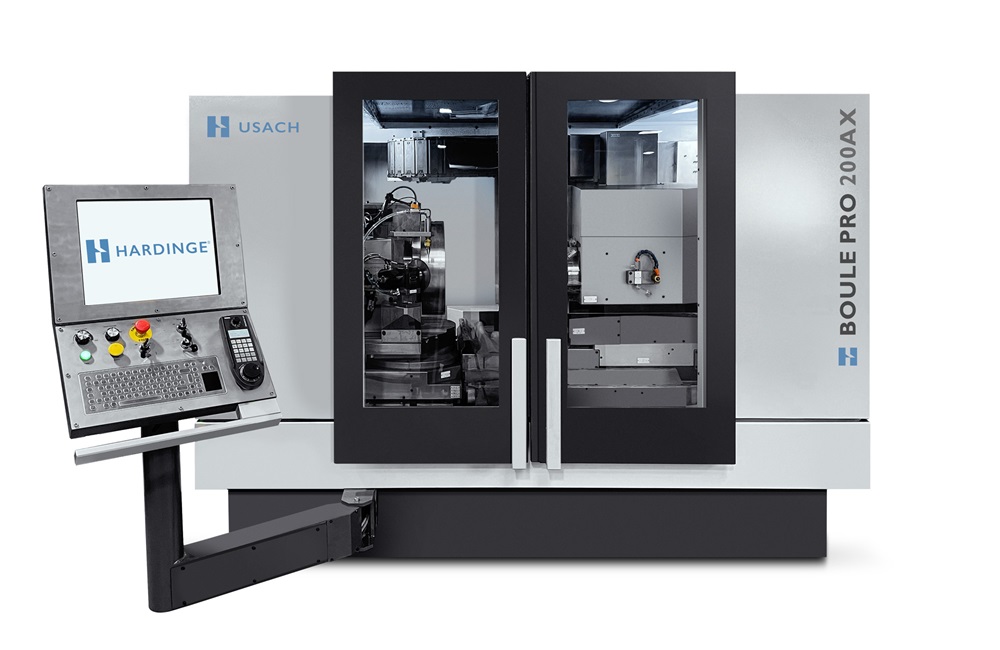
La rectifieuse BoulePro 200 AX permet de produire des galettes SiC en un temps record.
« Alors que les procédés traditionnels nécessitent plus de 24 heures », la rectifieuse BoulePro « ne prend que deux à trois heures lorsque le chargement et le déchargement sont automatisés, assure Jeff Gum, spécialiste des nouveaux matériaux chez Hardinge. Ce gain de temps contribue à une réduction globale des coûts de près de 70 % si l’on tient compte de la main-d’œuvre, de la surface de production, des rebuts, de l’efficacité de la capacité et des consommables. »
Porte-outil innovant
La machine est équipée d’un nouveau porte-pièce développé par le fabricant de dispositifs de serrage Forkardt, qui fait également partie du groupe Hardinge. Celui-ci permet de maintenir les boules en toute sécurité, sans colle ni intervention manuelle. « Ce porte-outil combine de manière unique un mandrin à griffes, parfaitement adapté pour serrer le diamètre extérieur non rond de la boule avant l’usinage, et un mandrin à dépression pour maintenir en toute sécurité la surface plane de la boule », détaille Hardinge.
Par ailleurs, la BoulePro est équipée d’un système de diffraction des rayons X intégré qui permet de déterminer l’orientation des cristaux au début de l’usinage. « Le système de diffraction des rayons X indique dans quelle mesure les surfaces cristallines doivent être ajustées lors de l’usinage final, explique Usach. Ce procédé d’alignement simultané sur deux plans (Single-Step Dual plane Compensation), issu du processus de développement et dont le brevet a été déposé entre-temps, est l’étape importante de l’usinage de la boule qui garantit que la boule est usinée dans l’orientation cristalline optimale. »
La BoulePro 200 AX est disponible sur le marché européen seulement depuis cet automne.

Déroulement du processus pour la fabrication d’un palet SiC : prépolissage du diamètre extérieur, polissage grossier du dôme, radiographie, finition du polissage du dôme dans l’orientation correcte, transfert à la contre-broche, élimination du côté germe, radiographie de confirmation, polissage final du diamètre extérieur et aplatissement/encochage.
à propos de fabrication
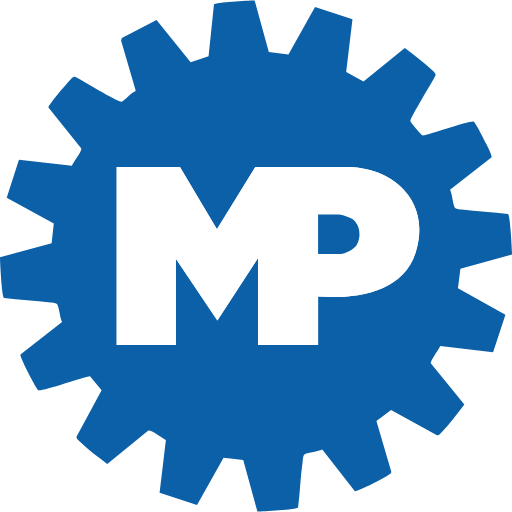