L’usinage de grandes pièces au service de l’e-mobilité
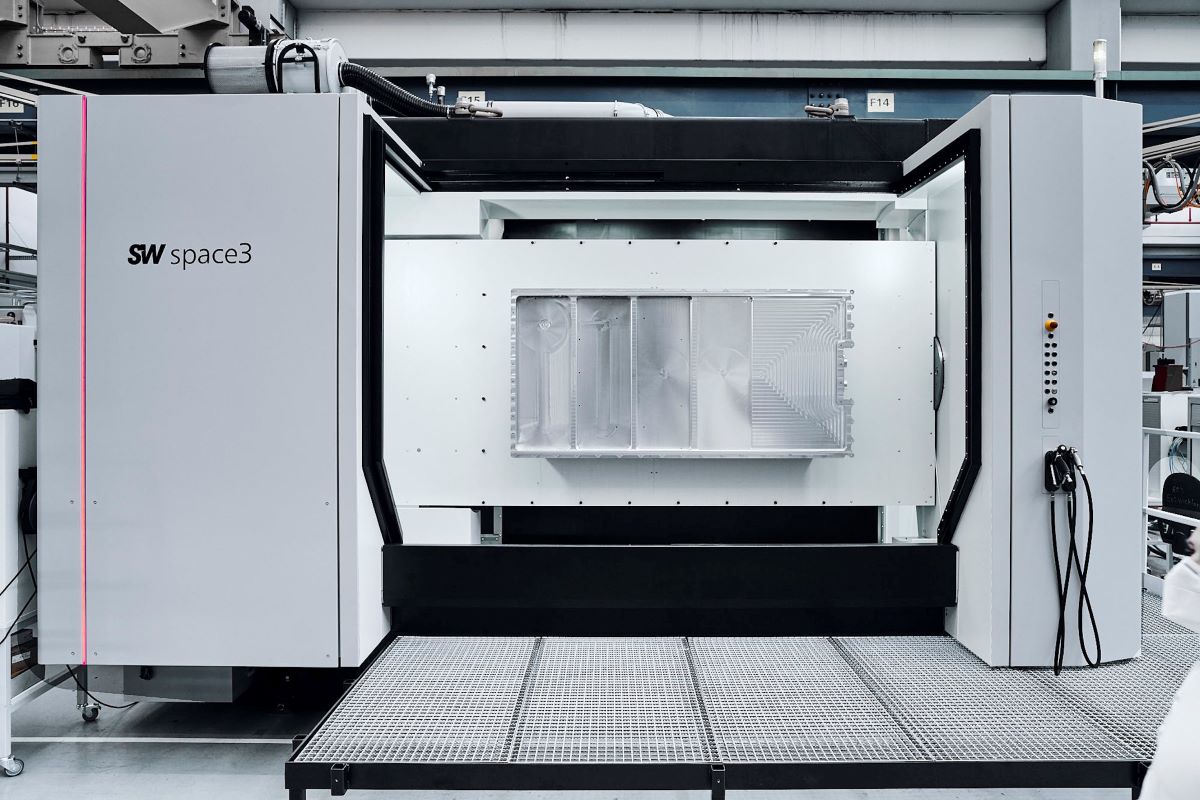
La transformation du marché automobile vers l’e-mobilité a conduit le constructeur de machines-outils SW à imaginer de nouveaux concepts de machines dédiées à l’usinage de pièces de très grande dimension. Après avoir lancé en 2021 la BA Space3 monobroche, SW poursuit sa quête de performance et annonce, pour la fin 2024, la BA Space3-22, une machine équipée de deux broches indépendantes, visant à améliorer encore l'efficacité et la flexibilité dans la production de gigas-pièces.
Le giga-casting consiste à fabriquer de grandes pièces structurelles en une seule pièce par coulée sous pression. Un défi qui ne concerne pas seulement les fondeurs sous pression. Après le succès de Tesla, des entreprises comme Volvo suivent le mouvement. Lors du giga-usinage, les composants structurels tels que le soubassement d’une voiture ne sont plus soudés, collés ou vissés à partir de nombreuses pièces individuelles, mais coulés en une seule pièce. Cela permet de réduire le nombre de pièces produites et de supprimer la plupart des opérations d’assemblage dans le processus de production, soit de réaliser des économies tout au long de la chaîne de production.
De plus, l’utilisation de giga-composants vise à réduire le poids d’un véhicule, ce qui est particulièrement recherché dans le domaine de l’électromobilité : un poids plus faible signifie une meilleure efficacité énergétique et donc une plus grande autonomie des véhicules. La production se heurte toutefois à des exigences complexes, à commencer par les énormes moules et leur thermorégulation, en passant par le processus de coulée lui-même, jusqu’au refroidissement ultérieur et à la déformation des composants qui en découle.
Grandes machines, grand besoin d’espace
Alors que certaines entreprises ont déjà développé de grandes machines spéciales pour la coulée sous pression, comme la gigapress de Tesla, la réalité est nettement différente en ce qui concerne le post-traitement CNC. Celui-ci s’effectue encore souvent sur des fraiseuses à portique issues de la construction de grandes pièces. « Pour les centres d’usinage CNC traditionnels, les pièces du domaine des giga-castings sont tout simplement beaucoup trop grandes, l’espace dans la machine ne suffit pas », explique Michael Kreuzberger, le chef de produit de SW. Il ajoute : « De plus, les installations issues de la construction de grandes pièces sont en fait trop grandes et surtout trop lentes. Un usinage efficace est à peine possible sur ces fraiseuses à portique monobroche, les temps d’usinage sont trop longs et le chargement et le déchargement prennent trop de temps. »
Les entreprises sont confrontées à d’énormes problèmes de place. Rien que les machines de moulage sous pression, nécessaires pour le giga-casting ont la taille d’une maison. Si l’on ajoute à cela des fraiseuses à portique, de nombreux halls de production atteignent rapidement leurs limites. Rares sont les entreprises qui, comme Tesla, ont la possibilité d’installer un nouveau hall de production de taille correspondante en rase campagne.
Fragilité des pièces
Même s’il y a suffisamment de place pour de grandes fraiseuses à portique, les temps d’usinage de telles machines sont un problème dans la construction automobile à cadence rapide, car les machines disposent généralement de vis à billes comme entraînement. Michael Kreuzberger explique : « En principe, dans l’usinage de l’aluminium, les temps morts sont nettement plus élevés que les temps d’usinage purs. Plus les pièces à usiner sont grandes, plus les axes d’avance doivent parcourir de longues distances et plus les temps morts sont importants, par exemple lors du changement d’outil. Les vis à billes présentent des accélérations et des vitesses plus faibles, ce qui entraîne des temps morts encore plus longs. » En bref, les machines du secteur de la fabrication de grandes pièces ne peuvent généralement pas fournir les cadences requises dans le secteur automobile exigeant. C’est précisément là que réside l’un des grands défis de l’usinage de giga-composants : atteindre, pour des pièces de cette taille, les mêmes vitesses que celles utilisées aujourd’hui dans l’industrie automobile.
Un autre défi est la fragilité des pièces. Comme des tensions apparaissent dans la pièce lors du moulage sous pression, les pièces moulées de grand volume sont sujettes à des déformations. De plus, dans les voitures électriques, les parois des pièces doivent être aussi minces que possible afin de réduire le poids. De ce fait, les pièces se déforment également plus facilement. « La précision de la machine n’est pas le problème, car aussi bien les grandes fraiseuses à portique que les petits centres d’usinage peuvent atteindre sans problème les précisions requises », commente Michael Kreuzberger. « Ce qui est beaucoup plus important, c’est que le dispositif de serrage dans le centre d’usinage et la technique de préhension de l’automatisation soient parfaitement adaptés à la pièce à usiner, afin d’éviter toute déformation pendant l’usinage ».
Une vitesse plus élevée grâce au moteur linéaire SW
Une solution pour la sensibilité des giga-composants lors de l’usinage : « Le dispositif de serrage est développé spécialement pour s’adapter exactement à chaque composant. Il est important d’être bien conseillé et de collaborer avec le fabricant concerné », explique le chef de produit. « Chez SW, nous avons notre propre département qui s’occupe exclusivement de garantir, en étroite concertation avec nos clients, une coordination optimale entre le dispositif de serrage et la pièce à usiner. » Les choses se compliquent dès qu’il s’agit d’atteindre les cadences requises. Il faut alors des machines adaptées, dotées d’une dynamique élevée et offrant l’espace nécessaire pour les giga-composants. Dans tous les cas, les utilisateurs devraient miser sur des installations équipées de moteurs linéaires. En effet, l’entraînement direct d’un moteur linéaire génère les mouvements souhaités sans éléments de transmission mécaniques. Il atteint ainsi des accélérations maximales et des vitesses de déplacement très élevées et fonctionne en outre sans usure.
« Les machines CNC les plus rapides du marché fonctionnent toutes avec des moteurs linéaires et des moteurs couples, y compris la plupart de nos propres machines », commente Michael Kreuzberger. « En outre, nous misons sur une structure dont le poids est optimisé. Nous réduisons ainsi les temps morts et minimisons les temps de cycle. Nos centres d’usinage atteignent des valeurs d’accélération de plus de 2 g et des vitesses d’avance rapide de 120 m/mn. »
Afin de rendre justement cette vitesse utilisable pour des pièces plus grandes, SW a innové et lancé la BA Space3 sur le marché en 2021. Ce centre d’usinage combine des cadences élevées avec l’espace nécessaire pour les grandes pièces moulées. Ce nouveau concept de machine mise sur une broche articulée et sur un seul axe Q qui permet de tourner la pièce à 180° et de l’incliner jusqu’à 16°.
La BA Space3 est équipée d’une table inclinée pour orienter la pièce et d’une seule tête de broche dotée d’un 4ᵉ axe pour usiner à des endroits qui nécessiteraient une rotation de la pièce. Sa plage de travail est impressionnante : 3 000 x 1 800 x 875 mm. Même avec des dimensions hors normes (pièce dans une enveloppe de diamètre 2,20 m par 3,50 m) pour les machines SW, la BA Space3 reprend les standards de vitesse des autres machines, qu’il s’agisse de la vitesse de déplacement des axes (120 m/mn), du temps de changement d’outils (4 secondes) ou encore de la répétabilité et de la précision extrêmes.
La nouvelle machine BA Space3-22 mise sur ses deux broches
Toutefois, seules des machines multibroches peuvent atteindre une vitesse encore plus élevée. Actuellement, il n’existe pratiquement pas de machines multibroches sur le marché pour les grandes pièces moulées. Mais SW annonce la BA Space3-22 qui introduit la bibroche dans la gamme Space pour réduire encore davantage le temps de cycle. La BA Space3-22 est équipée de deux broches totalement indépendantes, avec têtes rotatives et magasins d’outils indépendants. « Une particularité par rapport à nos autres machines multibroches : les deux broches fonctionnent de manière totalement indépendante », explique Michael Kreuzberger. « Nous utilisons deux unités autonomes à trois axes afin de permettre une flexibilité maximale pour différents composants. »
Pour les pièces de taille moyenne, les deux broches peuvent usiner chacune une pièce en parallèle. En revanche, pour les pièces de grande taille, où une seule pièce peut être placée dans la machine, les deux broches usinent simultanément deux zones distinctes de la même pièce et changent d’outil indépendamment l’une de l’autre. Le chargement en temps masqué via un support pivotant double réduit encore le temps de cycle. Ainsi, il est possible d’usiner des giga-pièces, comme le dessous de caisse arrière d’une Tesla, en seulement 1,5 mn, soit presque deux fois plus vite qu’avec des machines à une seule broche.
L’automatisation au service de la sécurité et de la productivité
Bien entendu, il ne s’agit pas de manipuler manuellement ces gigas-pièces. La gamme Space3 peut être automatisée pour le chargement-déchargement des pièces avec un robot 6 ou 7 axes monté sur rail au sol. Dans un contexte de temps de cycles longs, le robot alimente plusieurs machines afin de privilégier le travail en temps masqué.
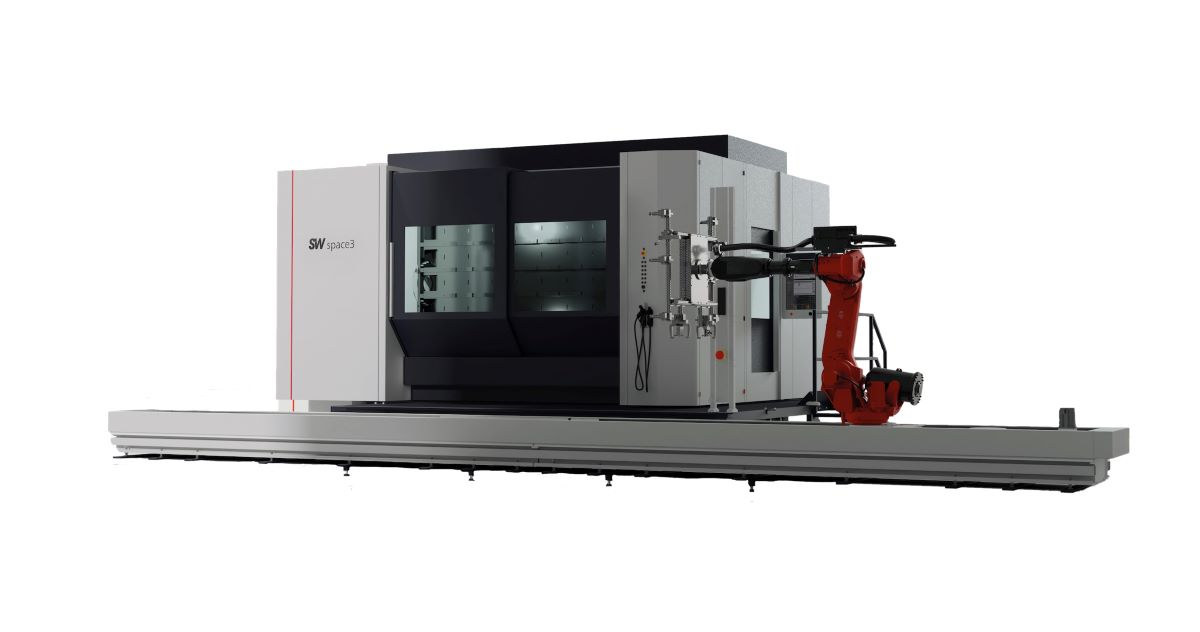
La gamme Space3 peut être automatisée pour le chargement-déchargement des pièces avec un robot.
« Avec le développement rapide de l’e-mobilité, le giga-casting va encore gagner en importance dans les années à venir », résume Michael Kreuzberger. « D’autres constructeurs automobiles étudient également les avantages et les inconvénients de l’utilisation de pièces coulées à grande échelle. Les fabricants asiatiques d’équipements d’origine (OEM), en particulier, misent déjà beaucoup sur le giga-casting et l’installent avec succès. Nous voulons apporter notre contribution pour que les avantages de ce procédé l’emportent et que les défis puissent également être relevés dans le domaine de l’usinage. »
à propos de fabrication
les plus lus
à lire aussi
Les nouveaux produits
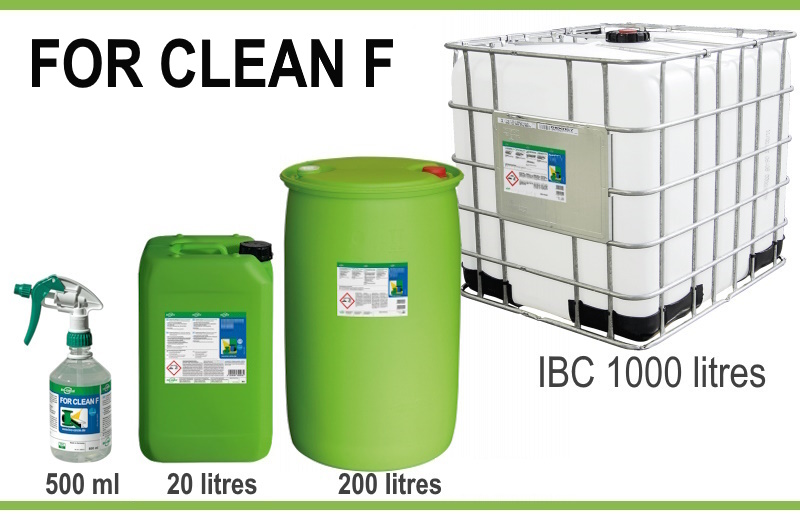
FOR CLEAN F de Bio-Circle, nettoyage industriel des pièces métalliques
Nettoyage écologique et économique de toutes les pièces métalliques, aluminium, non ferreux et autres matières pour l'industrie, la chaudronnerie, la mécanique et la plasturgie.