La rectification pour l’e-mobilité
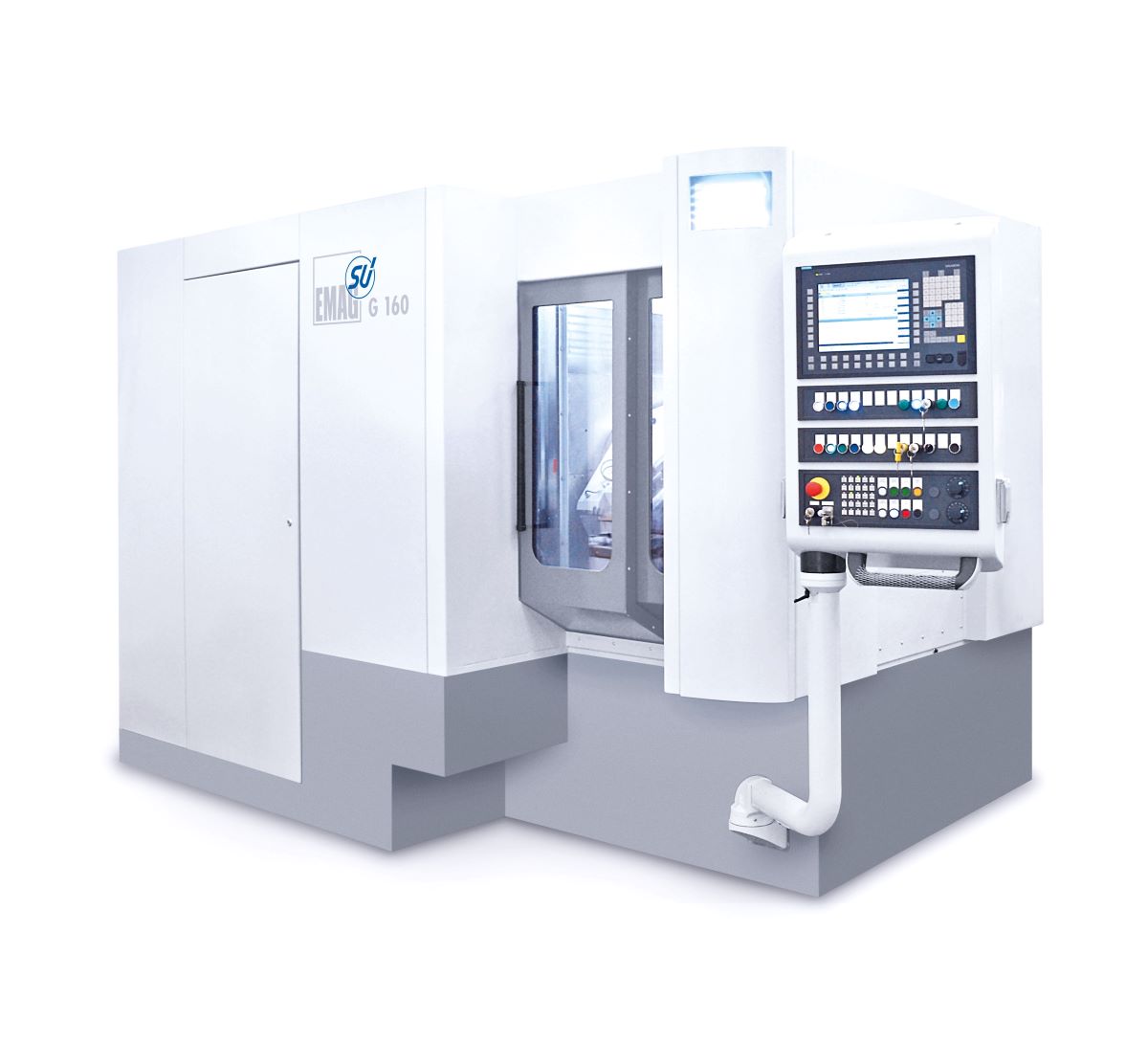
Dans l'industrie automobile, la précision et la sécurité des processus de fabrication est une exigence clé depuis des décennies. Emag Su, spécialiste des solutions de rectification, propose des technologies innovantes qui répondent à ces nouvelles exigences.
Avec l’avènement de l’e-mobilité, ces exigences augmentent encore, car de nombreux composants de moteurs électriques doivent être fabriqués de manière encore plus « parfaite ». La plupart du temps, il s’agit d’obtenir une qualité de surface maximale de l’ordre du micromètre afin d’éviter que les composants de la denture ne génèrent des bruits de fonctionnement. Les systèmes de rectification d’Emag Su veulent répondre à cette problématique, en offrant des solutions innovantes pour atteindre ces niveaux de précision.
Des solutions adaptées à chaque besoin
Les machines G 250 et G 160 se distinguent dans le domaine de la rectification d’engrenages, chacune ayant des spécificités adaptées à différentes applications. La G 160, par exemple, est idéale pour des pièces de petit diamètre, allant jusqu’à 160 millimètres et avec un module de trois. Elle est particulièrement rapide grâce à un système de deux tables porte-pièces parallèles qui se déplacent alternativement vers la meule. Pendant que l’une des pièces est usinée, un robot interne charge une nouvelle pièce et décharge la pièce finie, maximisant ainsi l’efficacité et réduisant les temps d’arrêt. La conception de l’axe de la G 160 joue un rôle crucial dans la production de surfaces parfaites, un critère important dans le secteur de l’e-mobilité. Au lieu d’un axe tangentiel traditionnel, la machine utilise les axes Y et Z pour créer un axe tangentiel « virtuel », ce qui réduit la distance entre l’outil de rectification et l’axe principal de la pièce. Cette innovation permet d’éviter les « fréquences fantômes », ou défauts de surface. Par exemple, pour l’usinage d’un arbre intermédiaire avec 21 dents, le temps total de production est de seulement 33 secondes, dont 25 secondes pour la rectification. De même, pour un arbre d’entrée avec 26 dents et un module de 1,6 millimètre, le temps de rectification est réduit à 28 secondes, démontrant ainsi la performance et la rapidité de la G 160.
La machine G 250, plus grande, se distingue par sa précision, ses temps de cycle réduits et sa fiabilité pour l’usinage de pièces allant jusqu’à 550 millimètres de longueur. Comme la G 160, elle est équipée d’une double table, permettant le chargement, le déchargement et la mesure des composants en temps masqué, ce qui optimise la productivité. Son mandrin de rectification est conçu pour accueillir des meules de différents diamètres, et sa construction rigide assure une stabilité thermique, garantissant une précision constante même lors d’opérations prolongées. Cette dernière permet également de passer rapidement d’un procédé de rectification à un autre en quelques minutes, une caractéristique particulièrement utile pour l’e-mobilité, notamment pour la rectification des roues motrices d’essieux. Ainsi, le temps total pour usiner une roue motrice est de 69 secondes, dont 58 secondes pour la rectification. La G 250 offre par ailleurs des performances remarquables lors de l’usinage de pignons avec des profils complexes, avec un temps de rectification de 28 secondes sur un cycle total de 33 secondes. Elle assure une qualité de surface conforme à la norme DIN-3962 (classe 4), garantissant ainsi des résultats précis et fiables.
Sky Grind : une technologie respectueuse de l’environnement
En outre, Emag Su propose aussi une innovation avec le procédé Sky Grind, qui permet une rectification entièrement à sec. Ce procédé présente un avantage économique, car l’installation de la filtration, du refroidisseur et autres (normalement nécessaires pour la rectification sous arrosage) sont supprimés, ce qui réduit l’investissement initial. De plus, la consommation d’énergie est également réduite. Cela étant rendu possible grâce à un système Dual-Tool avec deux broches d’outils différentes dans la machine : une pour la semi-finition par taillage et une pour la finition par rectification.
En pratique, pour un pignon automobile standard avec une surépaisseur de 100 micromètres sur les flancs des dents, le procédé Sky-Grind permet d’optimiser l’enlèvement de matière en deux étapes. Tout d’abord, 90 micromètres sont retirés par une opération de taillage par génération, qui assure une découpe rapide et efficace. Ensuite, seulement 10 micromètres supplémentaires sont enlevés par rectification, garantissant une finition de haute précision. Cette approche permet de combiner rapidité d’exécution et qualité de surface, tout en réduisant les coûts et la consommation d’énergie associés à la rectification conventionnelle.
à propos de fabrication
les plus lus
à lire aussi
Les nouveaux produits
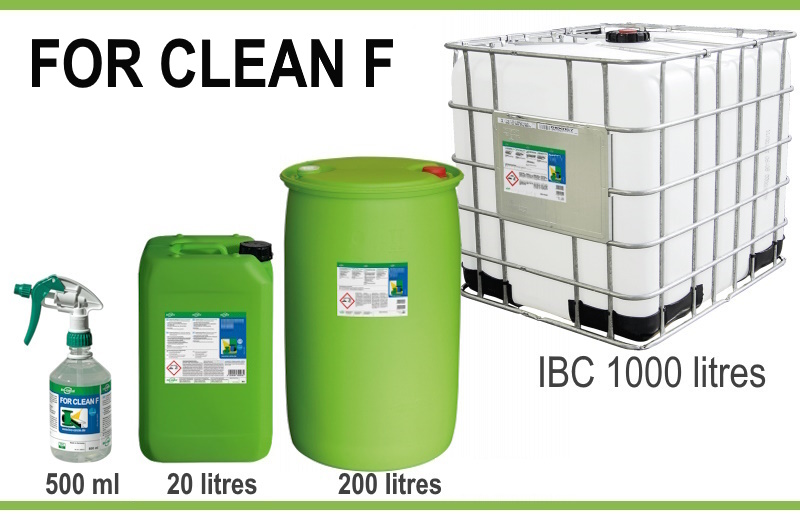
FOR CLEAN F de Bio-Circle, nettoyage industriel des pièces métalliques
Nettoyage écologique et économique de toutes les pièces métalliques, aluminium, non ferreux et autres matières pour l'industrie, la chaudronnerie, la mécanique et la plasturgie.