Les dernières innovations de Zeiss dévoilées à Paris
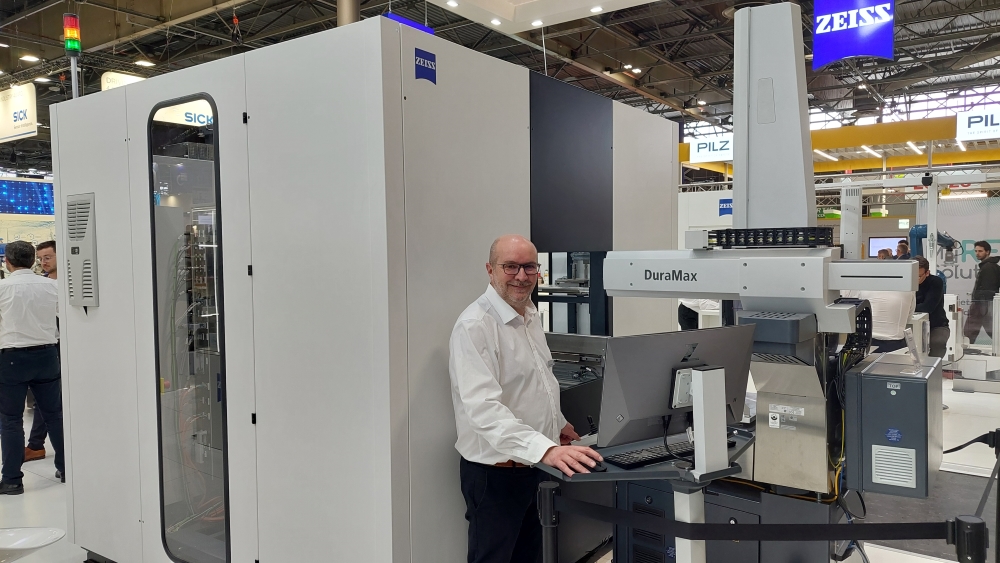
Ce sont plusieurs solutions de mesure et d’inspection à la pointe de la technologie qui étaient exposées lors du salon Global Industrie à Villepinte.
A l’occasion du salon Global Industrie, qui se tenait du 25 au 28 mars à Paris, le stand Zeiss dévoilait plusieurs nouveautés aux visiteurs du parc des expositions de Villepinte (Seine-Saint-Denis). Parmi lesquelles, le MultiLoad, une solution automatisée de chargement et de déchargement conçue pour alimenter jusqu’à trois machines à mesurer tridimensionnelles (MMT). Pouvant contenir 16 palettes, elle offre à l’entreprise de production la possibilité de travailler avec plus d’autonomie, la nuit et le week-end, « optimisant ainsi le flux de travail et minimisant les temps d’attente », note Pierre-Noël Campiglia, ingénieur applications chez Zeiss Industrial Metrology.
Le public a également pu découvrir la Prismo Fortis Aero. Cette MMT d’atelier, dont la précision de 0,7 micron est garantie dans un environnement entre 15°C et 40°C, est une version plus rapide que son modèle précédent. « Elle répond à une problématique de temps de contrôle, qui doivent être les plus courts possibles dans l’aéronautique, aujourd’hui, explique Mickaël Cichonski, responsable application et engineering chez Zeiss Industrial Metrology. Car le temps de mesure doit être le plus proche possible de celui d’usinage de la pièce. » Pour cela, la Fortis Aero affiche une vitesse de rotation de son plateau tournant de 400° par seconde au lieu de 60° par seconde. « On gagne 70 % de temps de contrôle en moyenne », souligne Mickaël Cichonski.
Plus faible consommation électrique
On observe que la machine est munie de deux barrières immatérielles, « qui permettent de garantir la vitesse maximale », précise Mickaël Cichonski. Ainsi, dès qu’un opérateur franchit la barrière, la machine passe du mode d’inspection rapide à normal, pour des questions de sécurité. D’autres modifications ont été apportées en réponse à la rapidité de la MMT. « Tous les espacements entre les carters ont été réduits, de manière à éviter les pincements ou écrasement de doigts », signale Mickaël Cichonski. Le bac de rangement des outils, situé sur l’avant de la machine, a été supprimé « de manière à éviter les problèmes de dos pour les opérateurs », poursuit-il. Pour réduire son empreinte environnementale, la consommation électrique de la commande numérique de la Prismo Fortis Aero a été réduite de près de 50 %. « Les modèles revisités gagnent aussi en durabilité et écoresponsabilité, grâce à la fonction PowerSaver qui déconnecte la machine de l’alimentation électrique après un temps prédéfini et met le contrôle en veille, la consommation est alors nulle », indique Zeiss.

Thomas Beuvier, référent tomographie chez Zeiss.
A cela s’ajoute le module AirSaver qui coupe également l’air comprimé après un temps prédéfini. A notre que le contrôleur C99m peut réduire la consommation de 68 % dans un cycle de test normal. Enfin, l’acoustique de la machine passe de 70 à moins de 50 décibels.
Etait exposé le Metrotom 6 Scout, le système de tomographie conçu pour détecter les défauts internes, mesurer les caractéristiques internes et externes et vérifier l’assemblage des pièces. « C’est la plus précise de la gamme, avec des résolutions jusqu’à 3 µm et une incertitude de mesure de 3 µm aussi », explique Thomas Beuvier, référent tomographie chez Zeiss. Son plateau peut recevoir des pièces de 240 mm de diamètre par une hauteur de 200 mm, pesant jusqu’à 5 kg. La machine utilise un logiciel commun (Zeiss Inspect) pour les scanners optiques et la tomographie, « ce qui permet aux utilisateurs de bénéficier d’une passerelle et de pouvoir se rattacher à une solution qu’ils connaissent déjà, qu’ils viennent du monde de l’optique ou de la tomographie », note Thomas Beuvier.
Mesure de forme
Enfin, c’est la ScanBox 5110 qui a impressionné les visiteurs de Global Industrie. La solution de mesure robotisée à lumière structurée a été conçue pour réaliser des inspections automatisées de pièces de grande taille ou de lots de petites pièces. « On inspecte principalement la forme d’une pièce, parce que bien souvent la forme fait la fonction », explique François Lambert, responsable des systèmes optiques chez Zeiss Industrial Quality and Research, soulignant que la cellule peut aussi bien mesurer des pièces de la taille d’un ressort de touches de clavier à la pale d’hélicoptère.
Sur le stand Zeiss, c’est une pièce en injection aluminium qui était utilisée dans la ScanBox. Un support de parechoc, appelé aussi « shock tower » est scanné par la tête de mesure ATOS fixée au bout d’un bras robotique Fanuc. « Ici, on vient savoir si j’ai bien la même épaisseur partout, décrit François Lambert. On va avoir un scan de l’intérieur et l’extérieur de la pièce, de manière à vérifier si on a suffisamment de matière. On vient contrôler la forme, mais aussi que les distances et les positions des différents formes sur la pièce soient conformes à ce qu’on attend. Avec cette cellule, on peut à la fois réaliser des mesures d’épaisseur, du contrôle de forme et du dimensionnel, pour savoir si les éléments ont la bonne taille et s’ils sont placés au bon endroit. » La ScanBox est piloté par le logiciel Inspect, qui peut générer des rapports détaillés.

François Lambert, dans la cellule de mesure robotisée Zeiss ScanBox.