Accélérer l’impression 3D grâce à la simulation
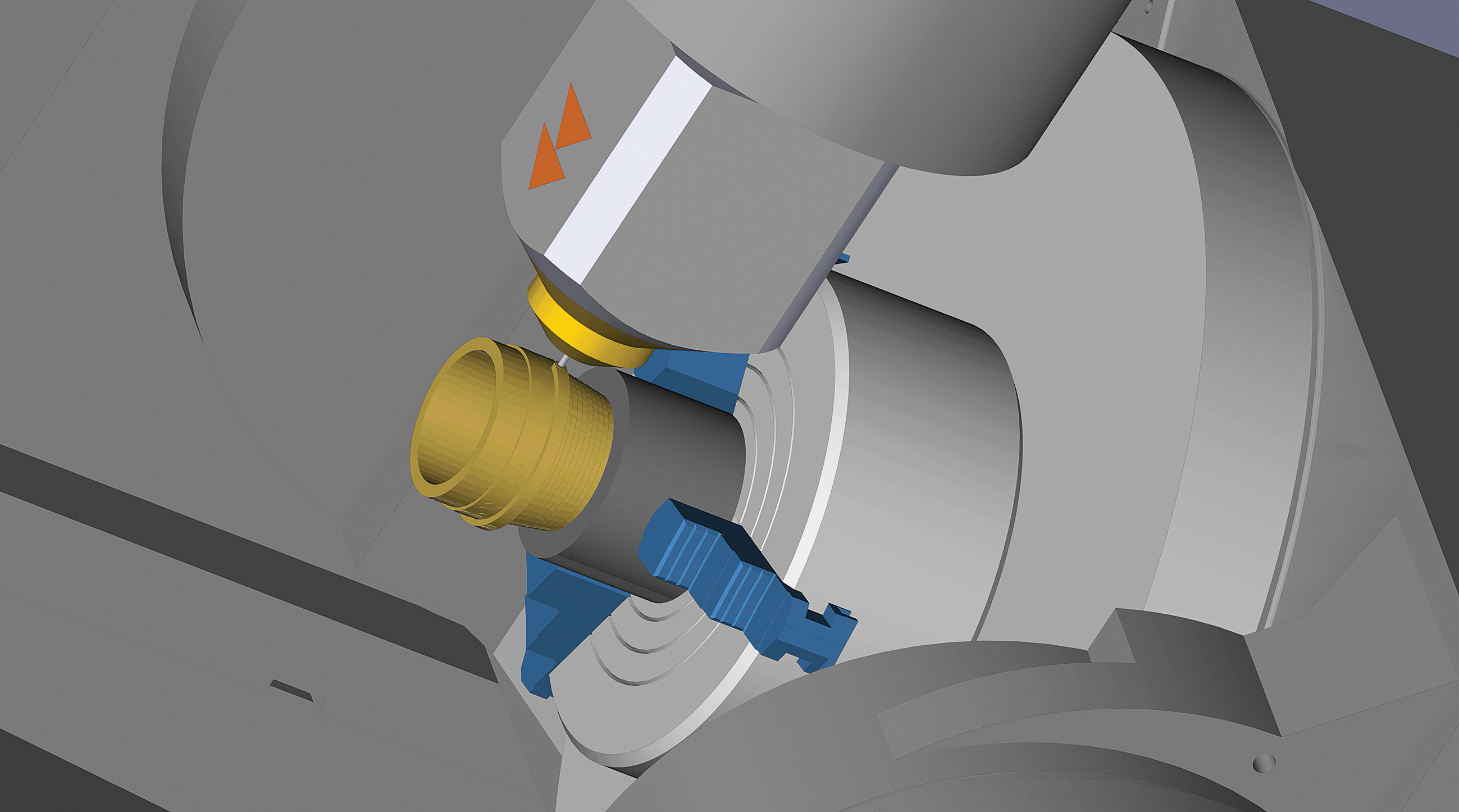
L’équipe Esprit CAM est engagée dans des projets de recherche afin de développer des solutions de simulation de parcours d’outils dédiées aux technologies additives.
Connaissant toutes les contraintes liées à l’additif et désireuse de fournir de nouvelles technologies à leurs utilisateurs finaux, l’équipe Esprit CAM s’est engagée dans des projets de recherche nationaux et internationaux, en collaboration avec les centres de recherche ou les entreprises principalement dans les secteurs de l’aérospatiale/aviation et de l’énergie, afin de développer des solutions de simulation de parcours d’outils dédiées aux technologies additives. Aujourd’hui, ses équipes continuent de contribuer à la recherche sur les technologies additive, en fournissant un outil puissant pour continuer à développer les connaissances.
L’année dernière, en étroite collaboration avec Mazak, Esprit a réalisé des tests pour valider les trajectoires des parcours d’outils additifs. Ces tests ont permis de valider des cycles sur des machines à 3 et 5 axes. Et ils ont donné de bons résultats. Les essais se poursuivent pour évaluer les technologies prometteuses en fabrication additive et en robotique.
Deux parties ont été choisies pour valider respectivement les applications à 3 et 5 axes. La partie 3 axes a été conçue pour valider des trajectoires simples et le comportement du dépôt de matériau sur des angles aigus. Pour ce faire, la pièce comprenait des pointes, des pentes et une poche au milieu. L’idée principale était de tester les capacités hybrides, en construisant une pièce en additif dans la forme de base de la pièce, puis la finir en usinage soustractif. Pour tester un cycle à 5 axes, l’équipe a choisi une pièce de valve. Comme pour la pièce à 3 axes, l’idée était de construire un modèle de base sur mesure pour économiser de l’argent, des matériaux et du temps, par rapport à l’utilisation de barres. Ces deux pièces d’essai ont été construites à l’aide d’une machine Variaxis J-600 et d’un robot Yaskawa équipé d’une tête Fronius et d’une technologie de fabrication additive par arcs métalliques. Dans les deux cas, l’équipe Esprit a constaté que le réglage précis des paramètres de travail était la clé d’un bon dépôt, avec de bons résultats proches des trajectoires simulées.
Les processus additifs
Dans l’environnement FAO, la simulation de cycles additifs permet aux utilisateurs finaux de vérifier les parcours outils, y compris les résultats de la simulation thermique et le temps de parcours. L’intégration de l’environnement machine complet dans la simulation présente l’avantage supplémentaire d’une capacité de prise en compte des machines, permettant de détecter et d’éviter les collisions dans l’environnement virtuel, avant qu’elles ne causent des problèmes dans le monde réel. Au fur et à mesure de l’évolution de la technologie, la FAO évoluera elle aussi. En étant au premier plan et en développant la technologie de la FAO additive au même rythme que l’industrie des additifs, Esprit promet de rester à la pointe du progrès.
à propos de fabrication
les plus lus
à lire aussi
Les nouveaux produits
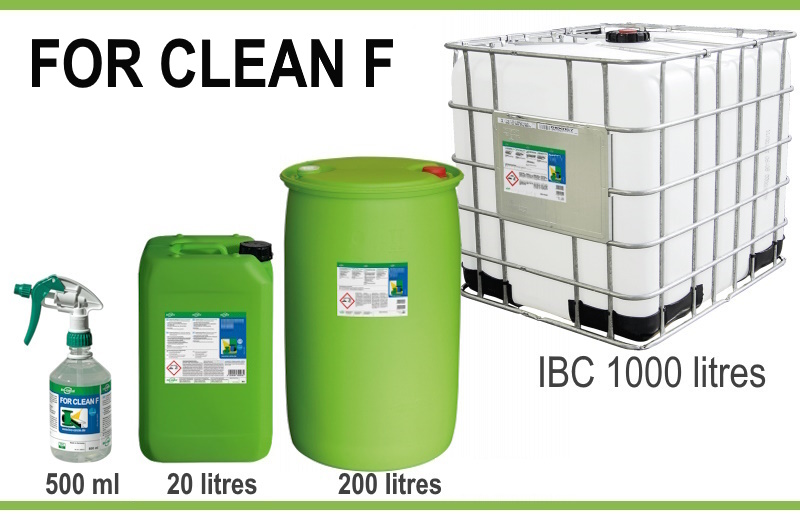
FOR CLEAN F de Bio-Circle, nettoyage industriel des pièces métalliques
Nettoyage écologique et économique de toutes les pièces métalliques, aluminium, non ferreux et autres matières pour l'industrie, la chaudronnerie, la mécanique et la plasturgie.